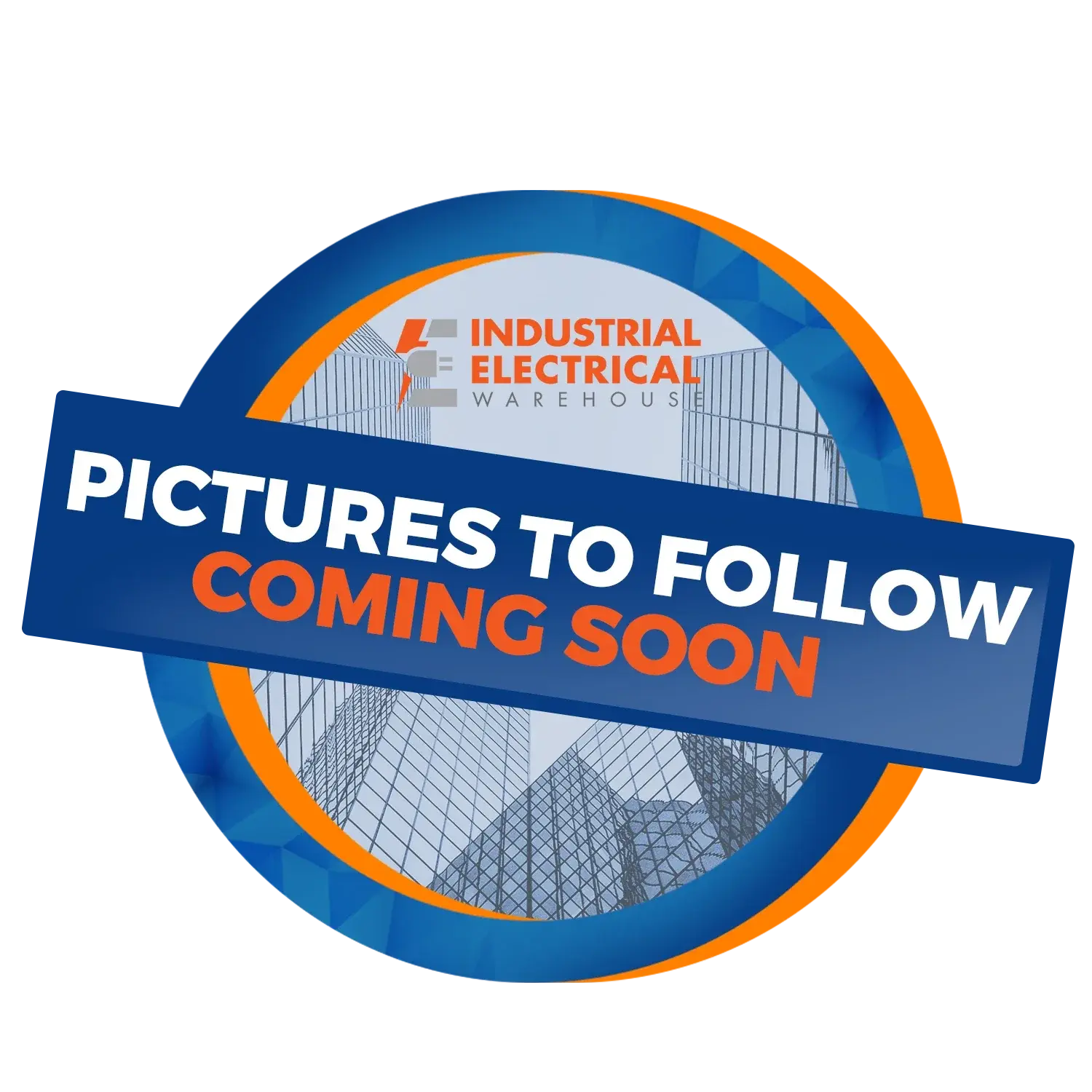
Sensor Cables
28 products
Showing 1 - 28 of 28 products


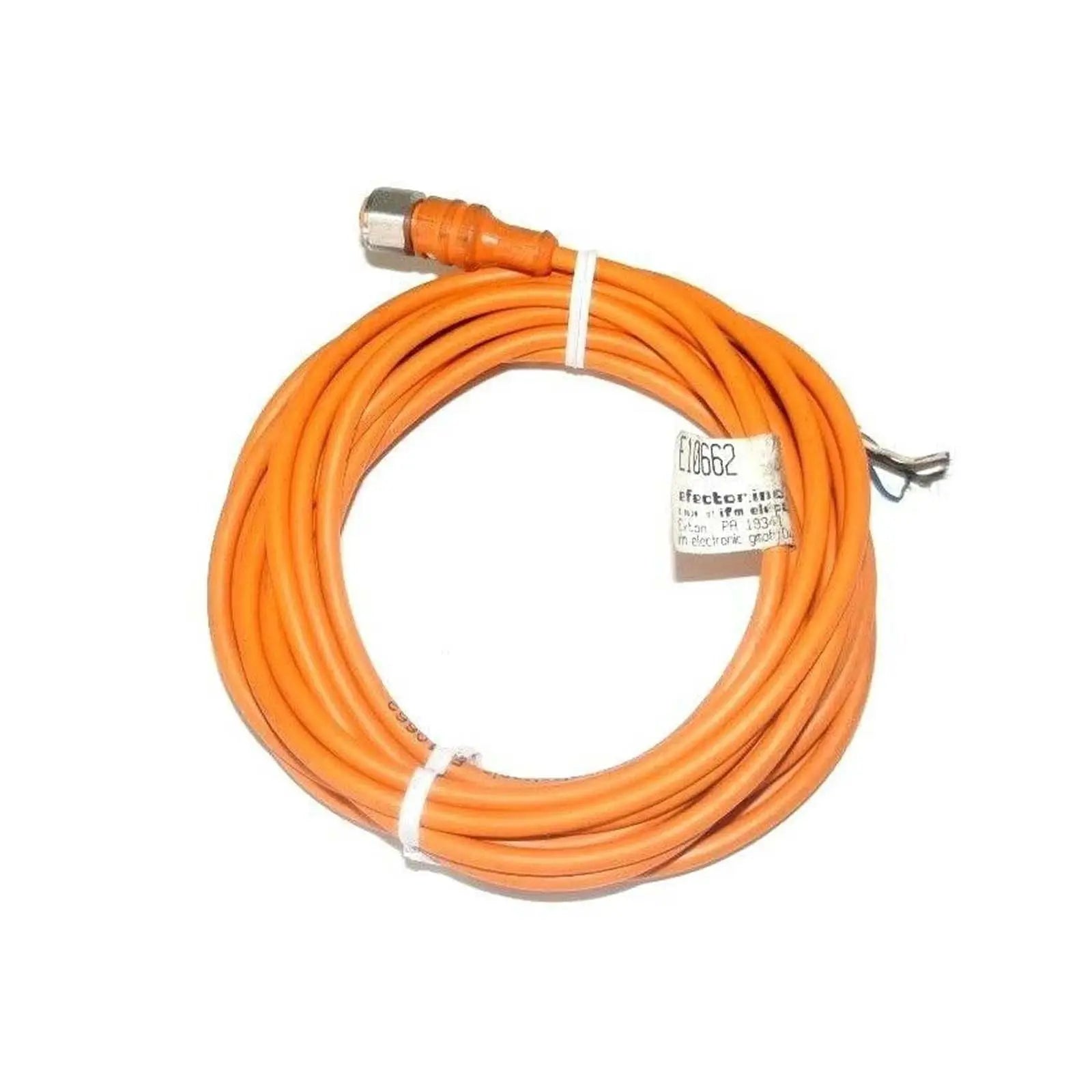
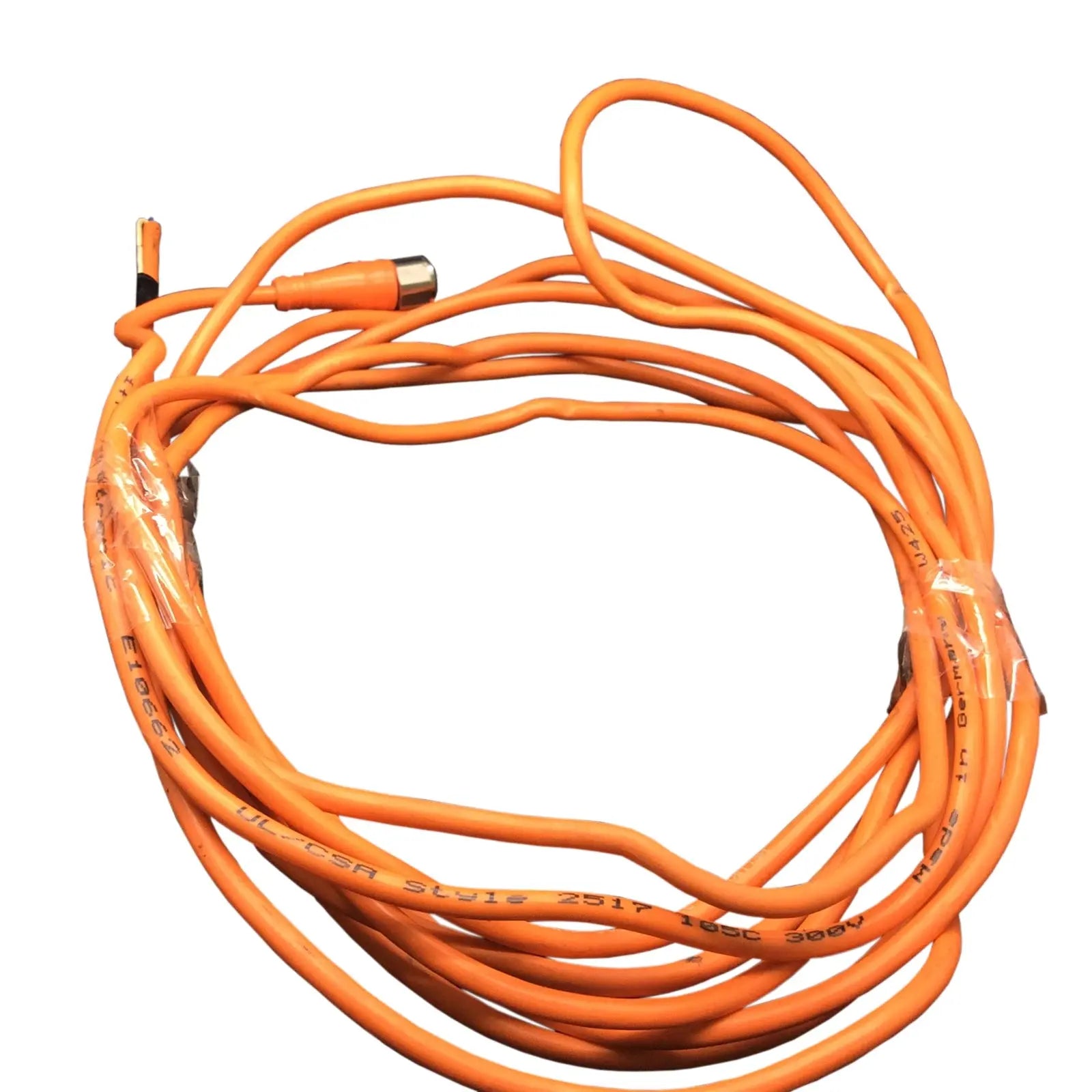
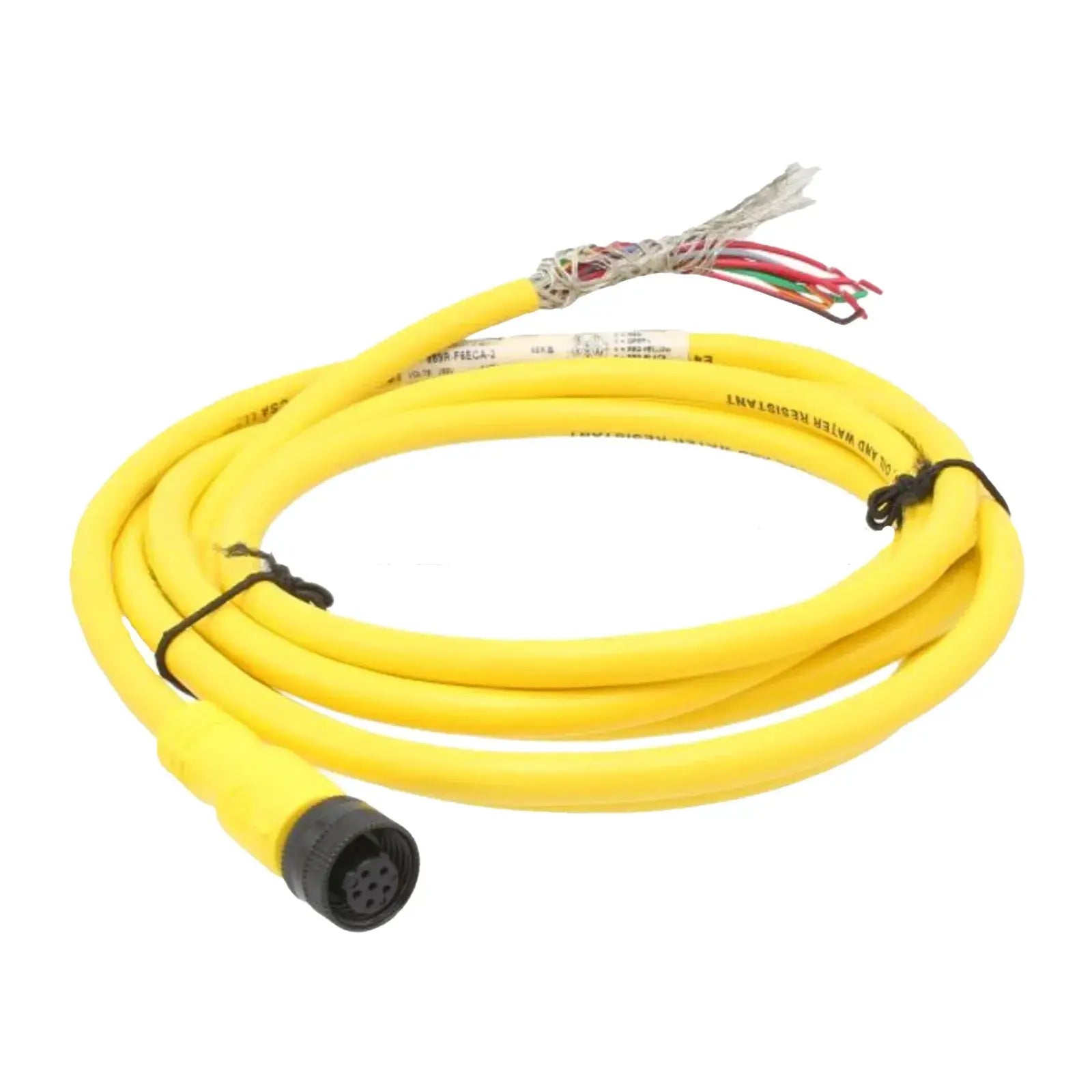

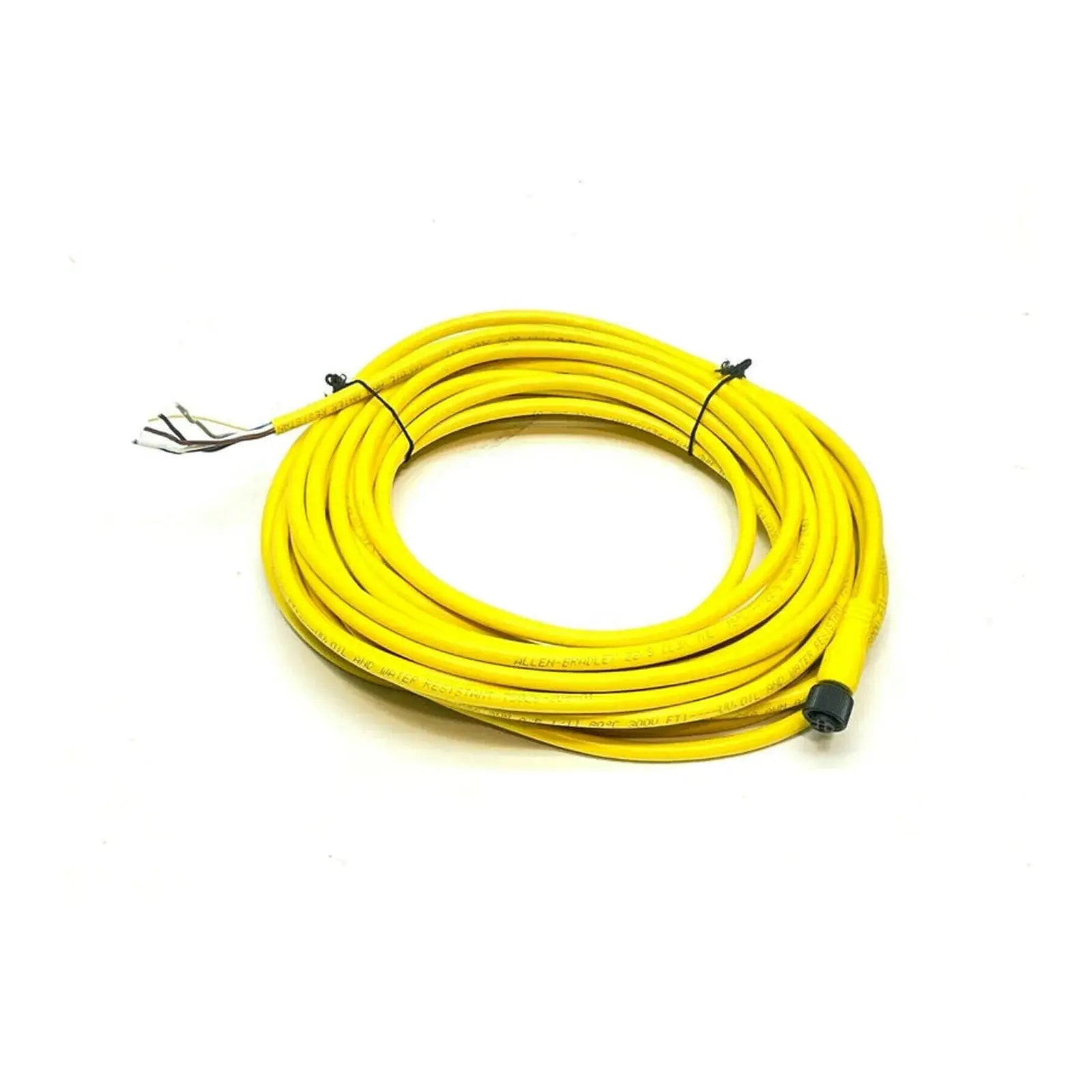

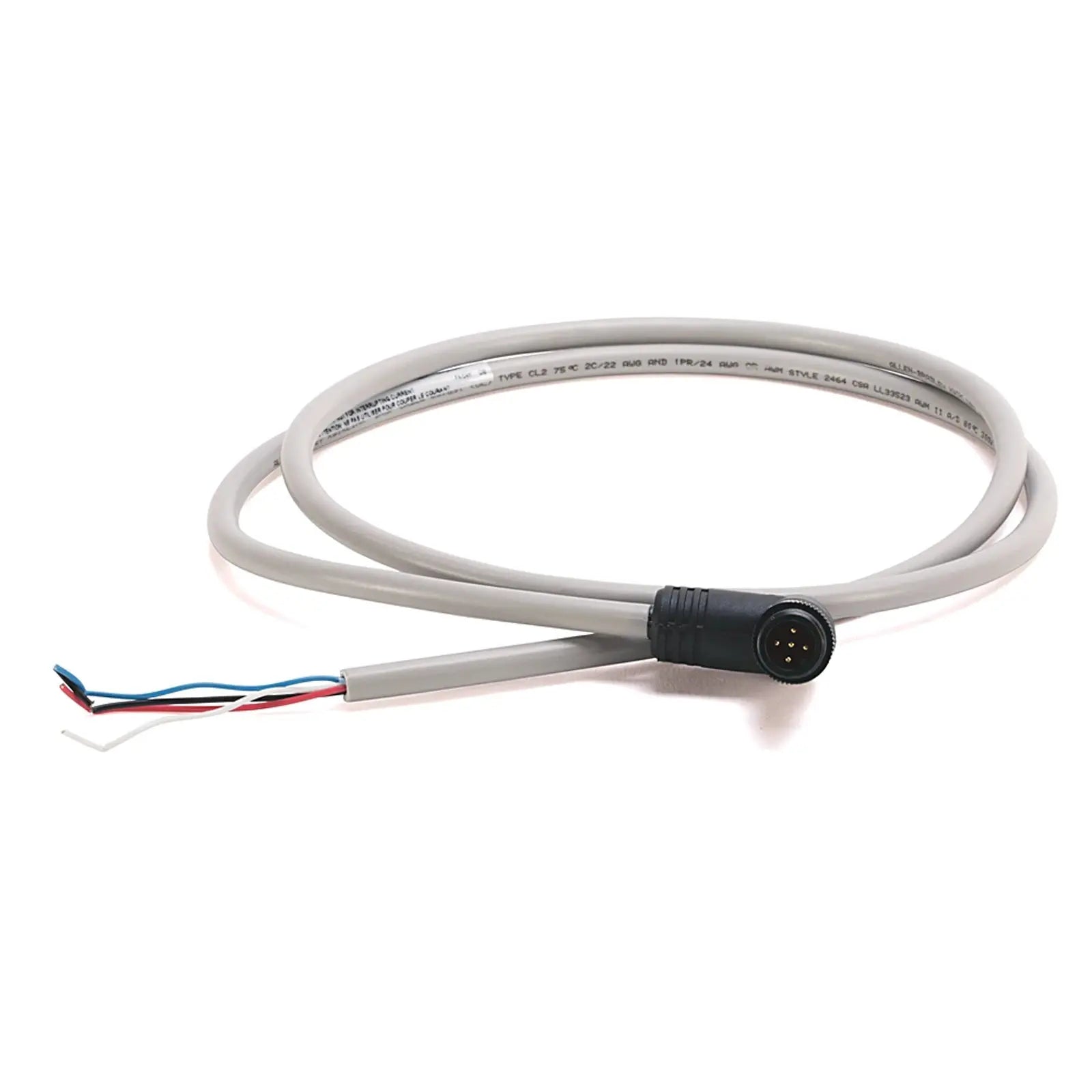
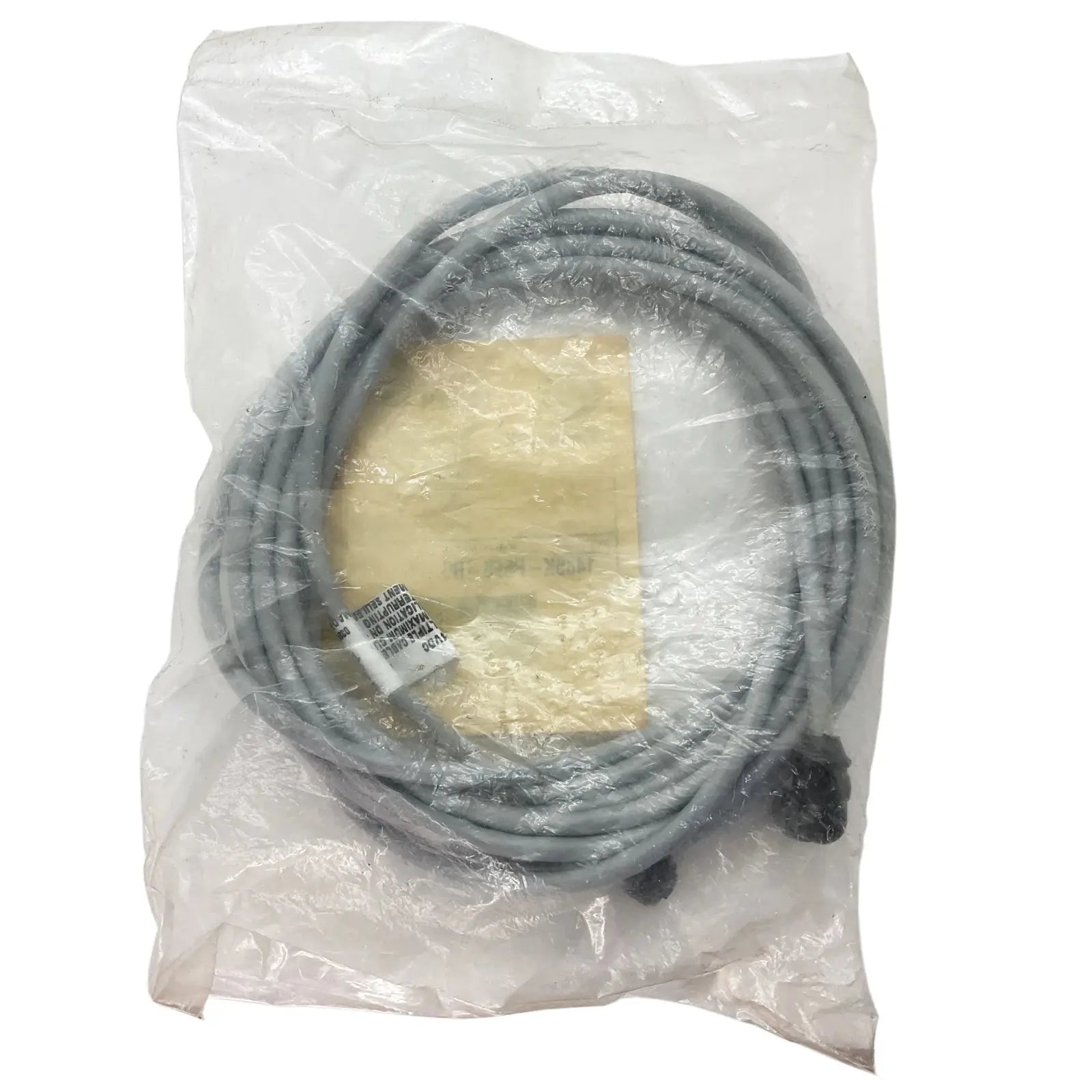
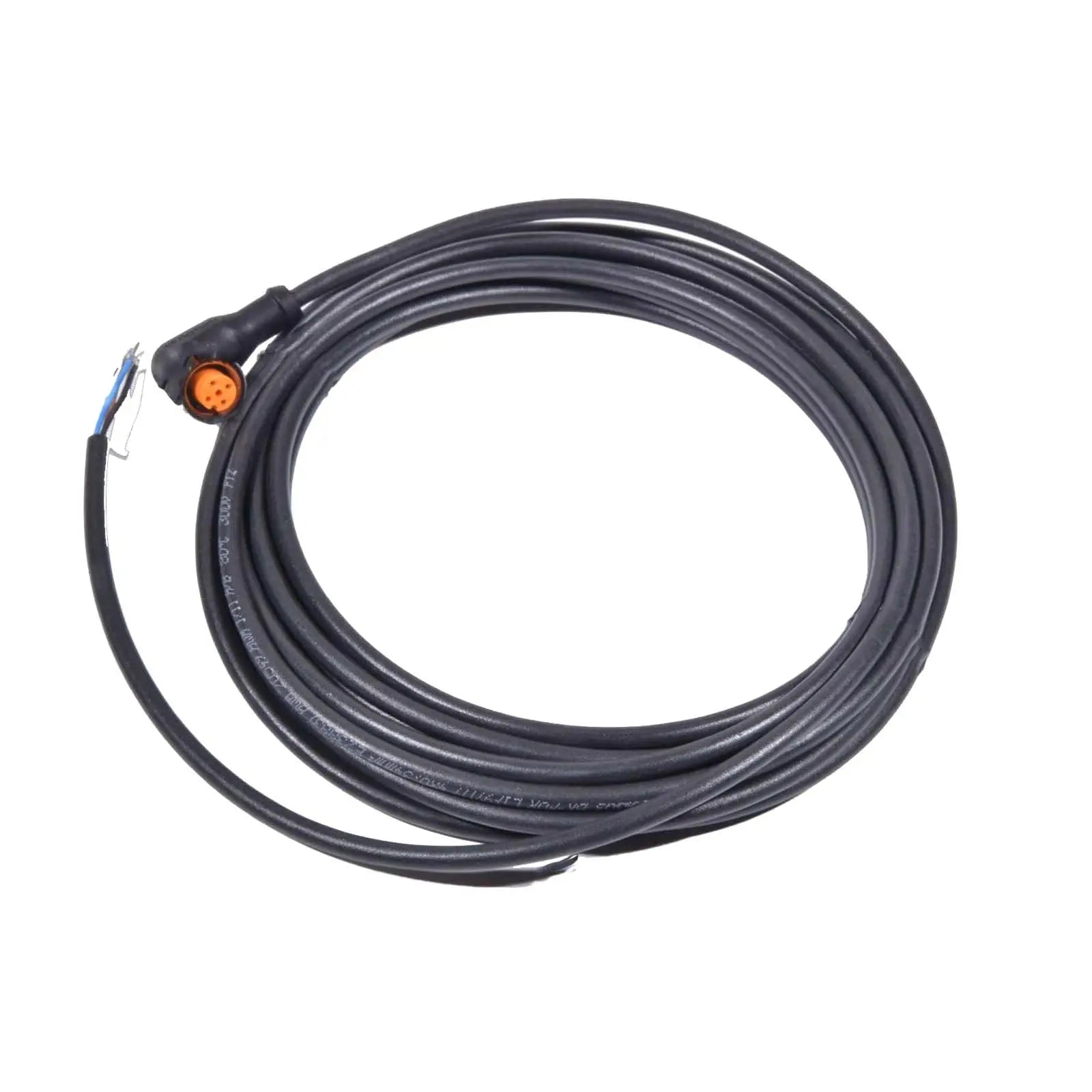
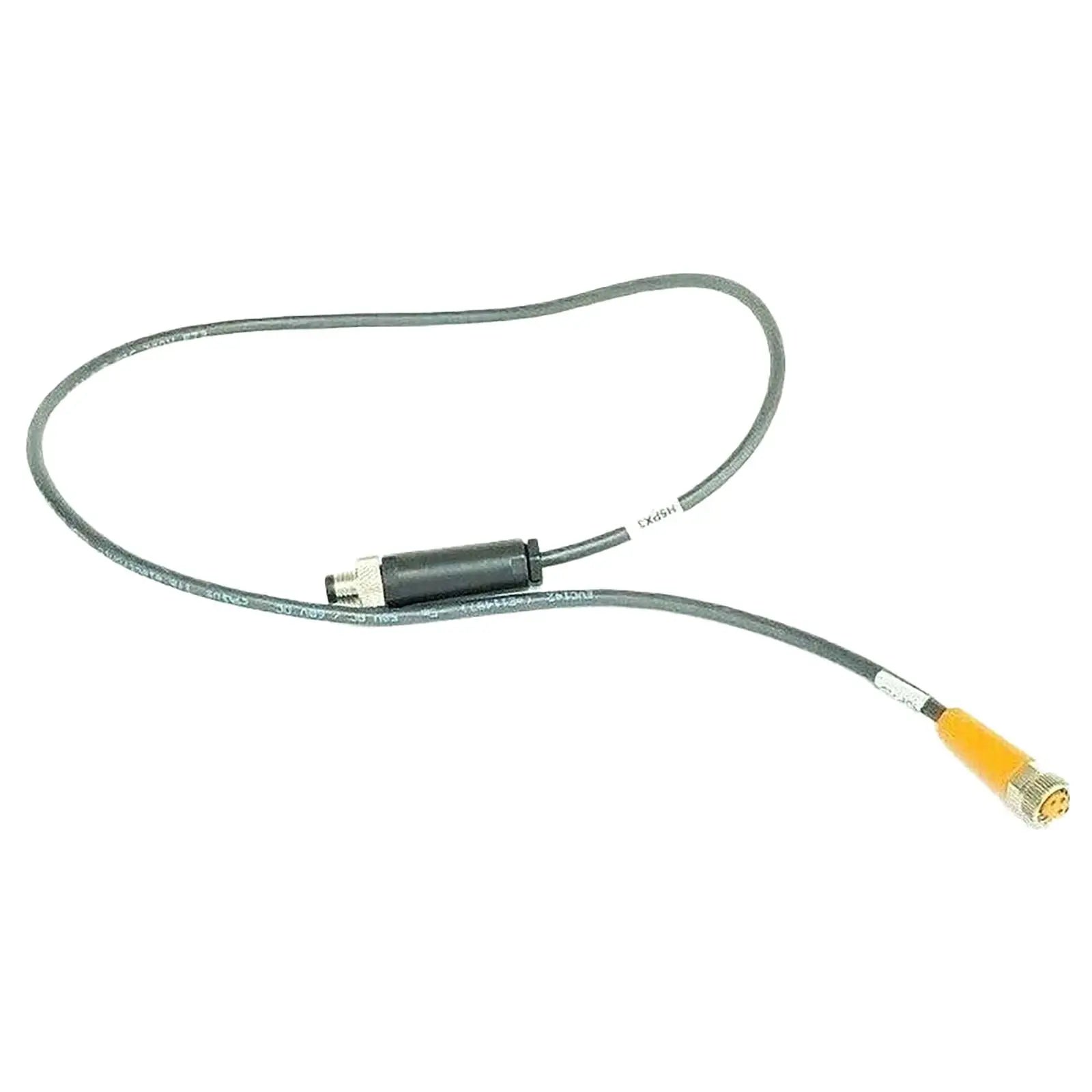
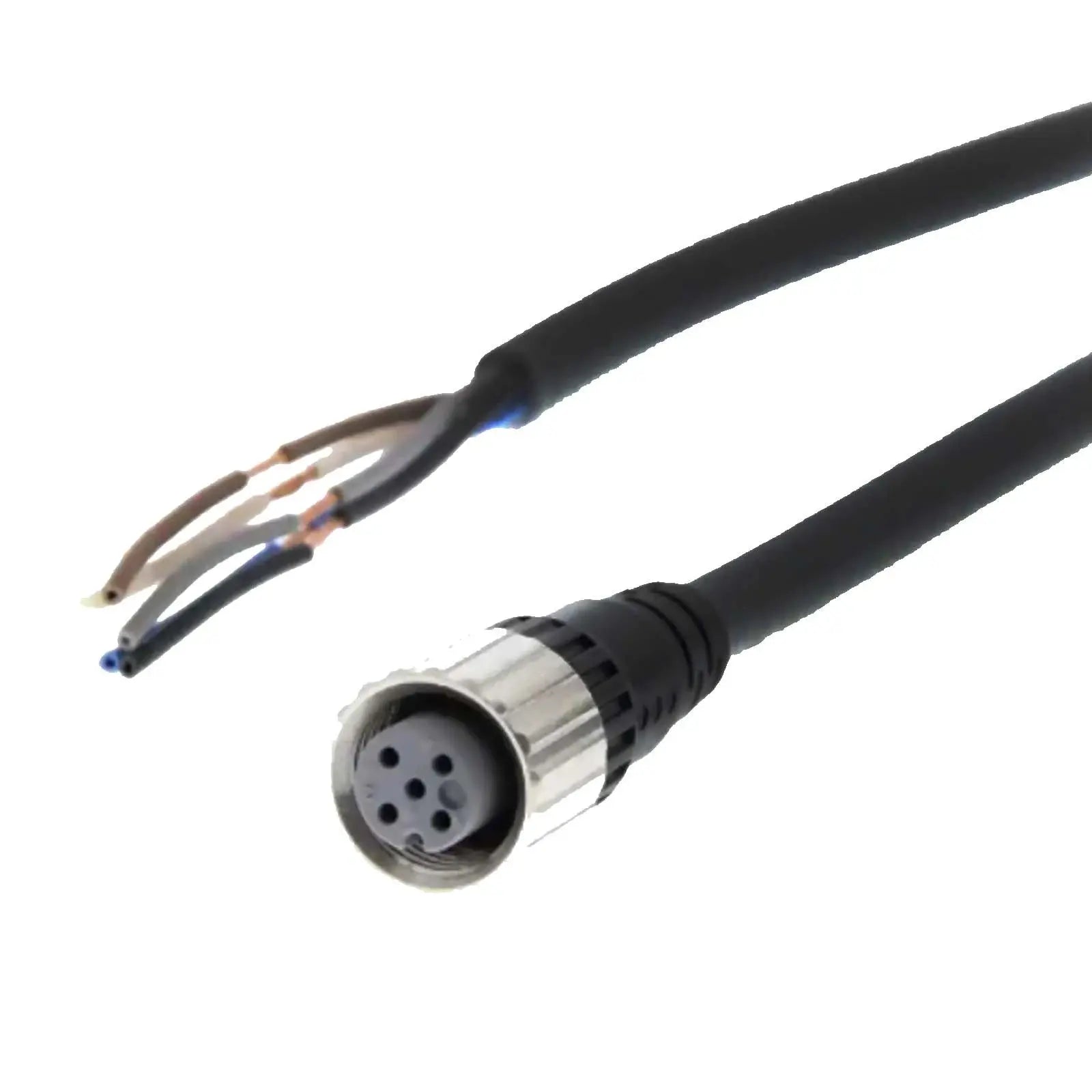
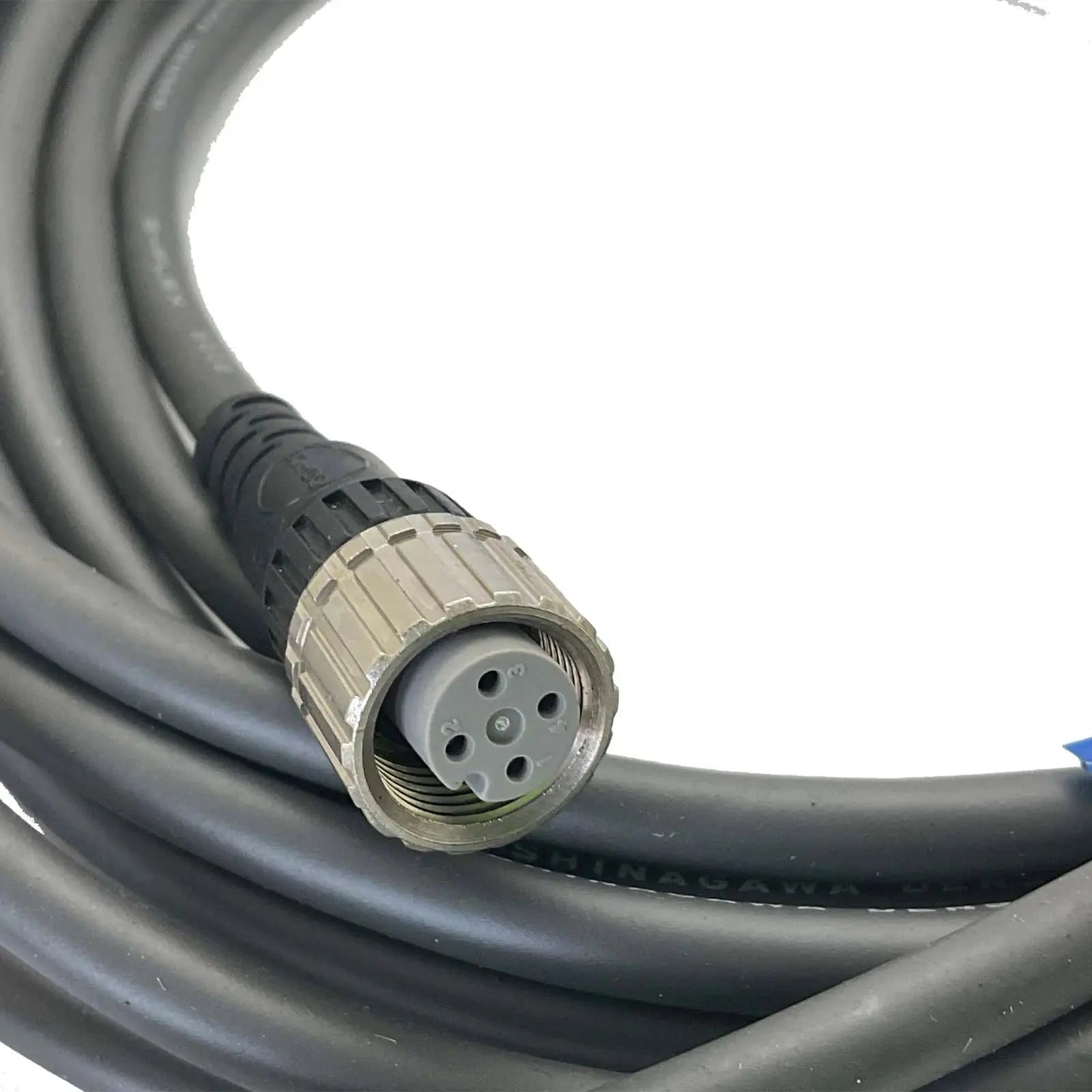
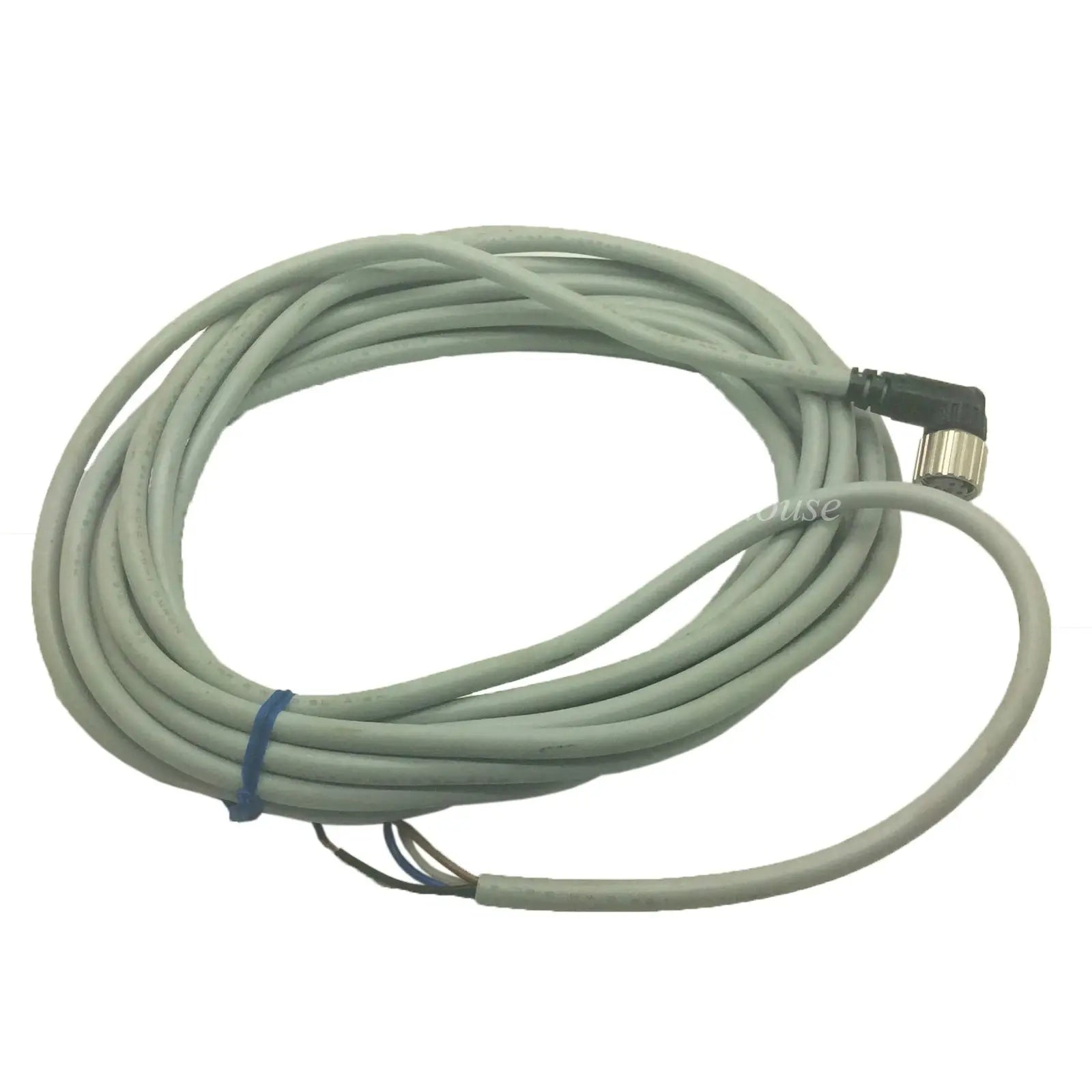
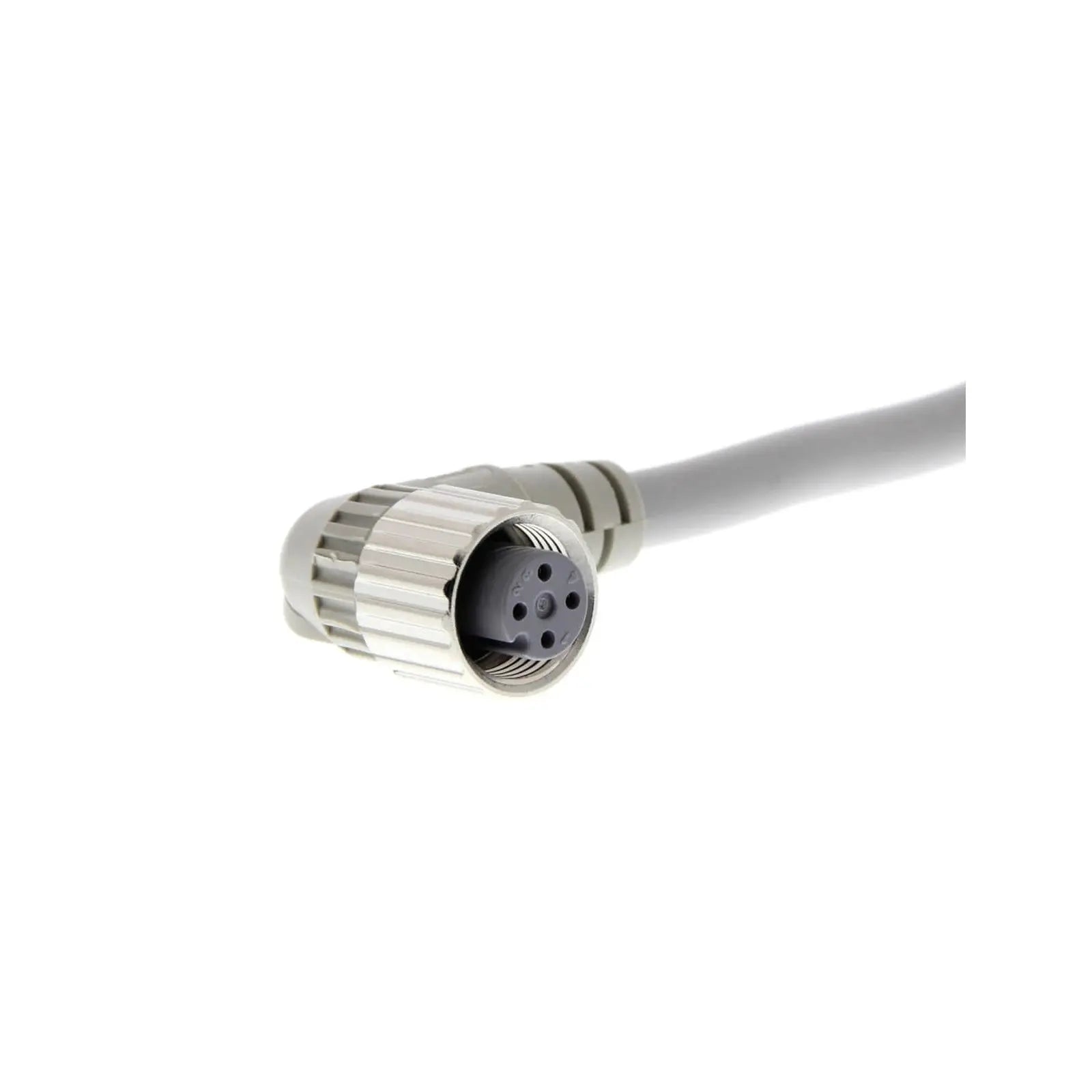





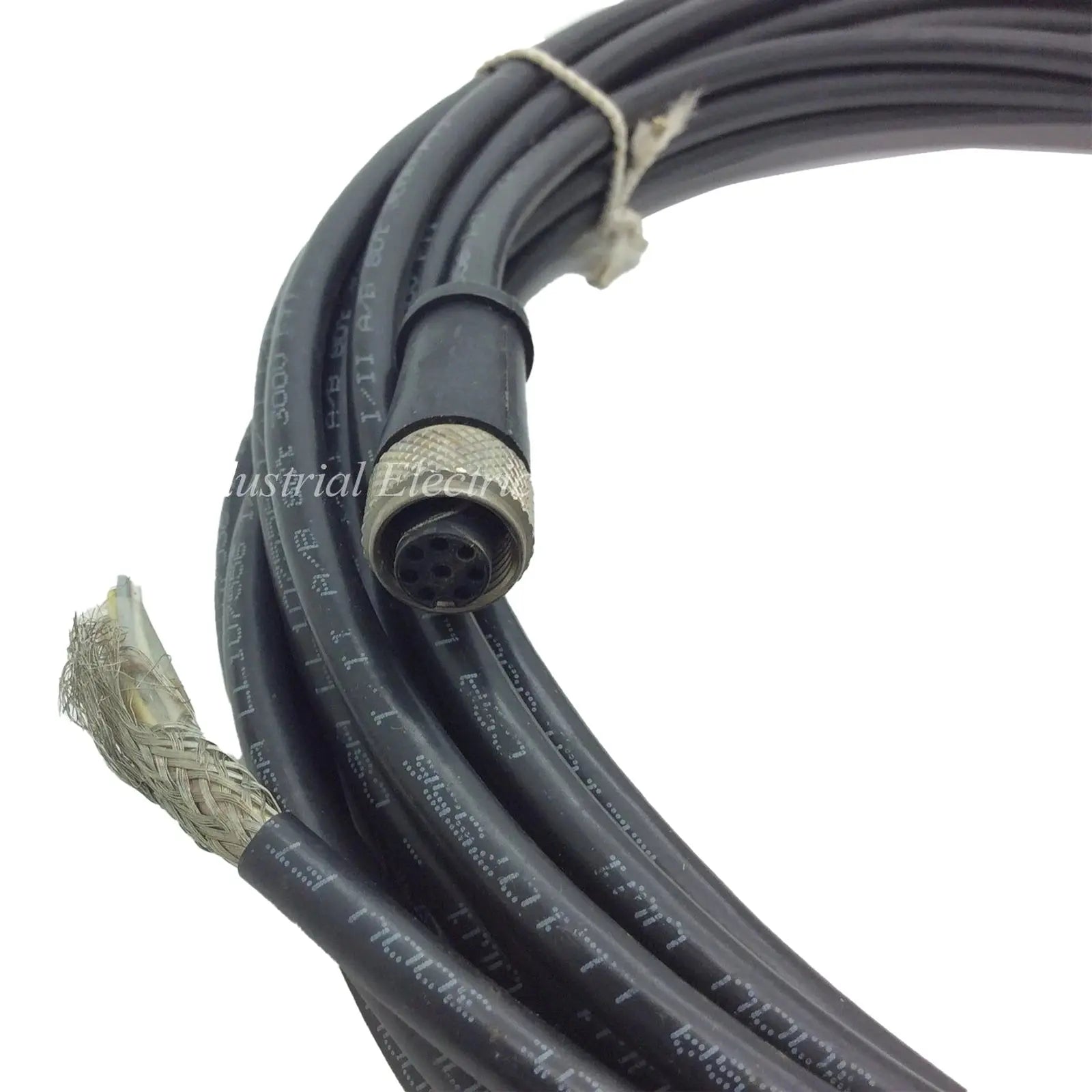
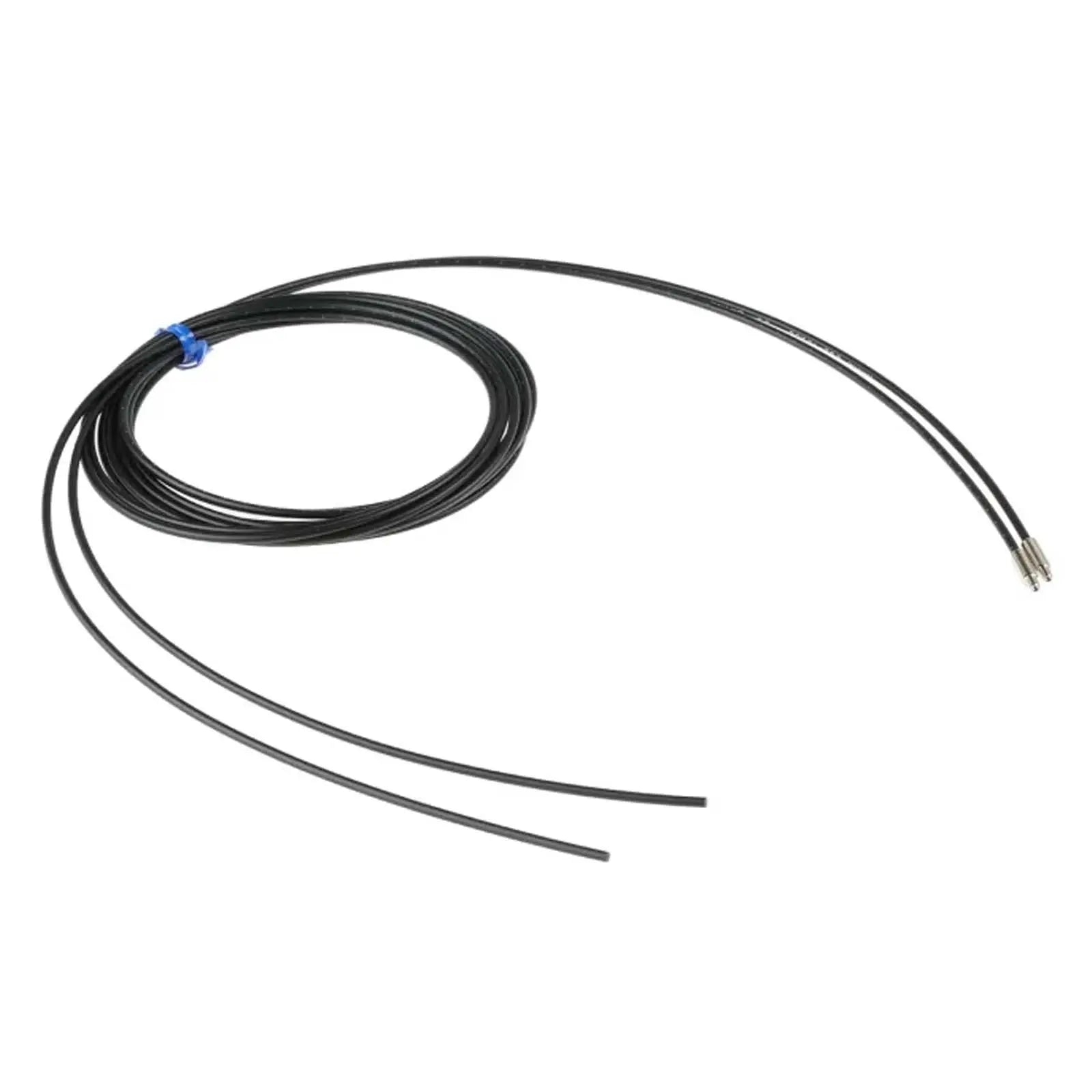

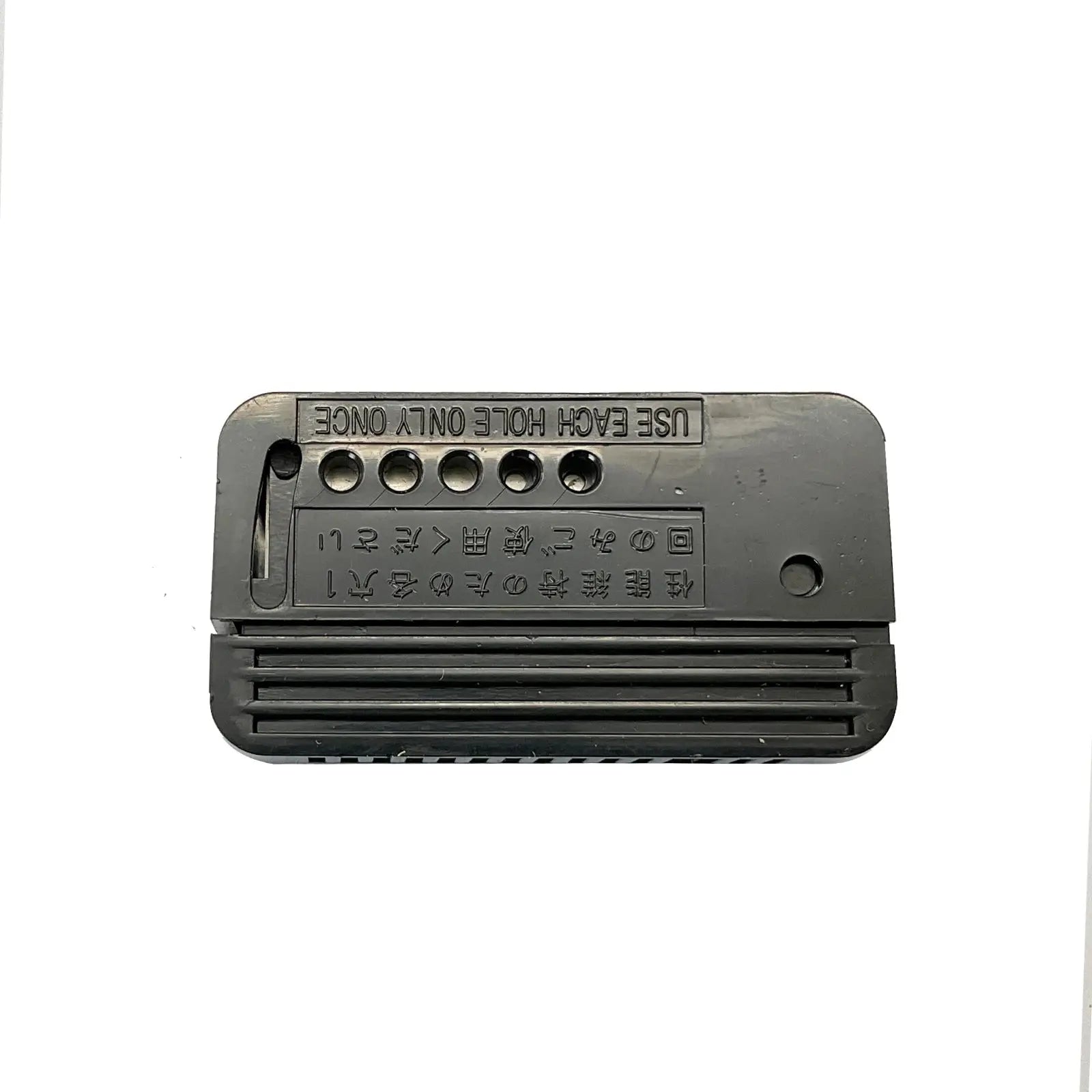
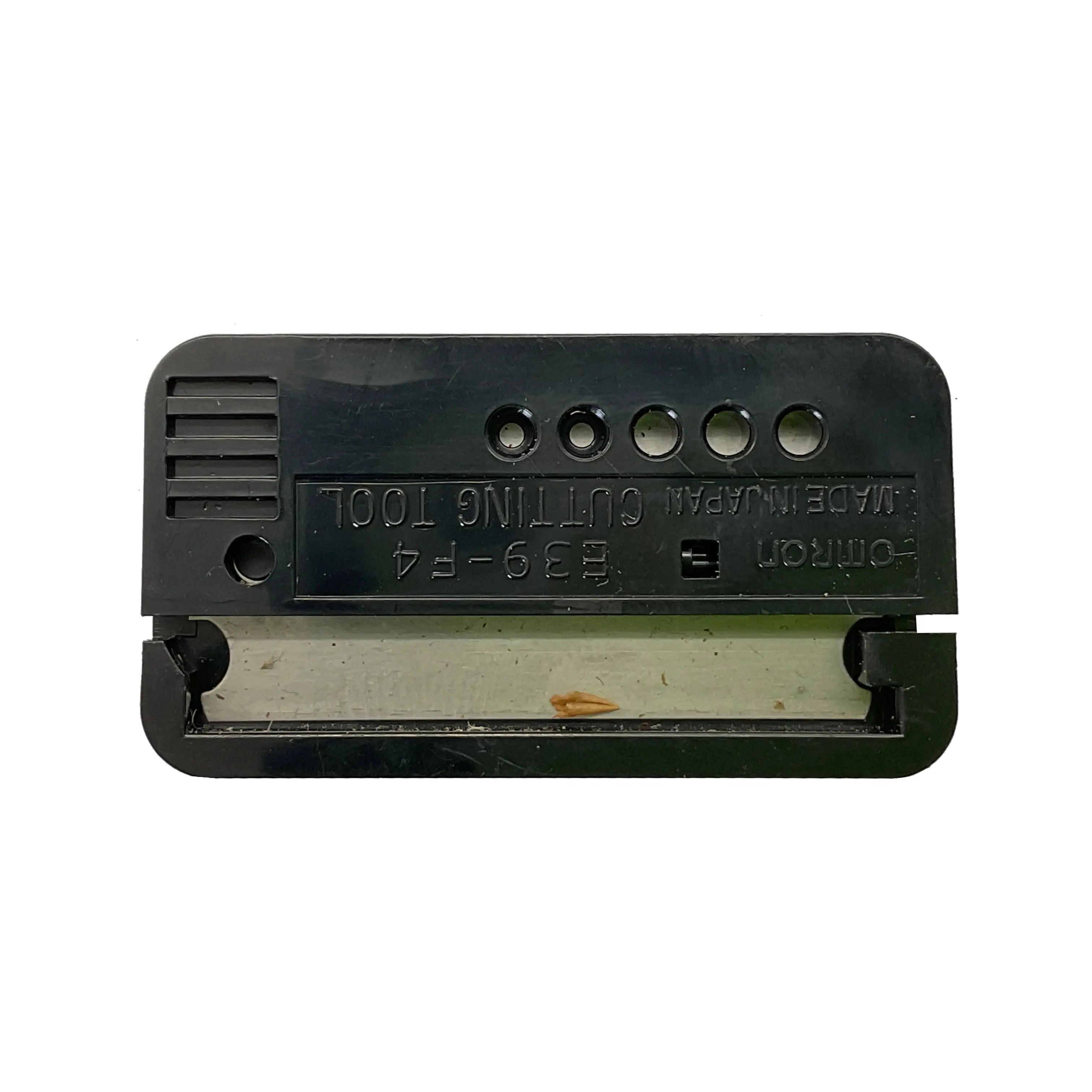

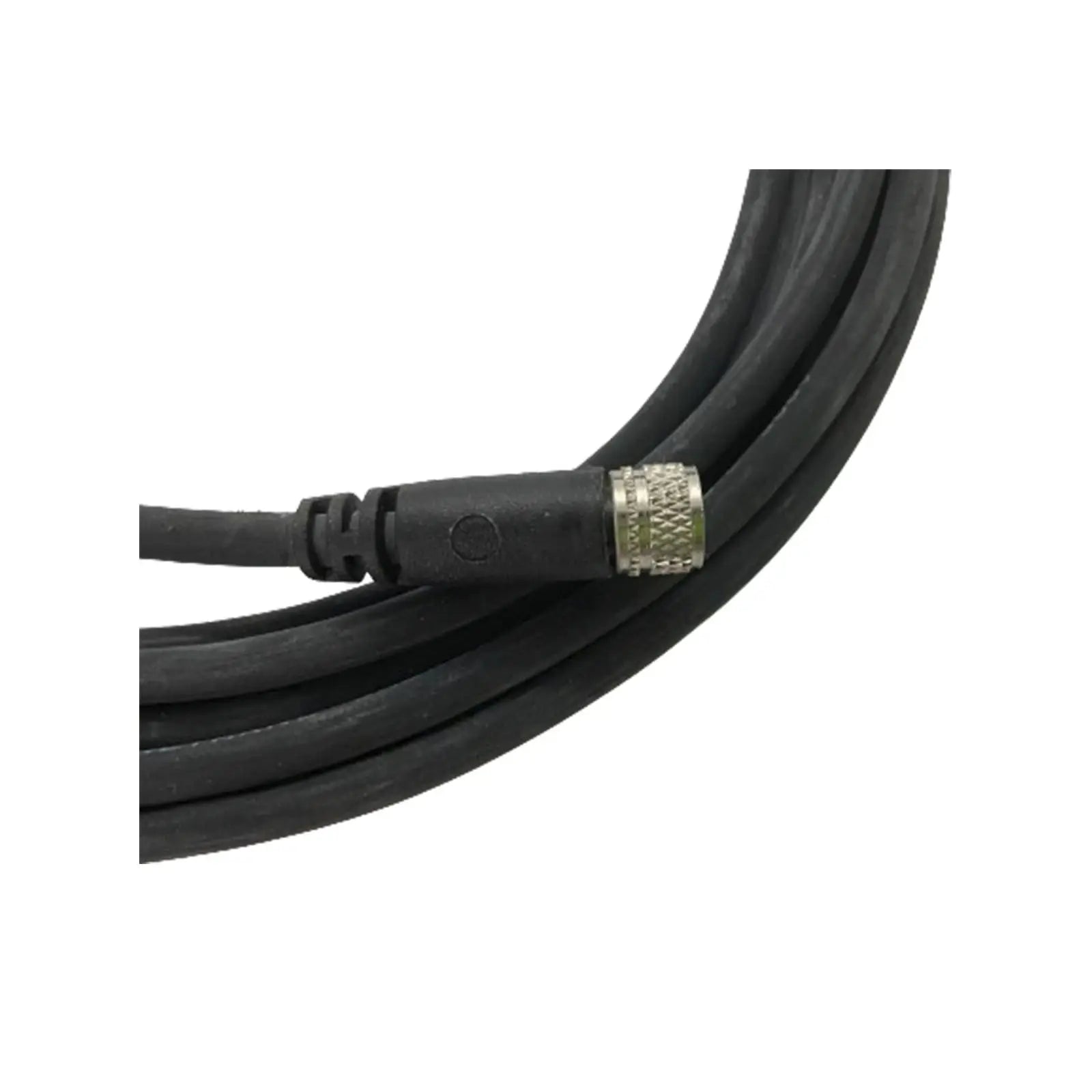
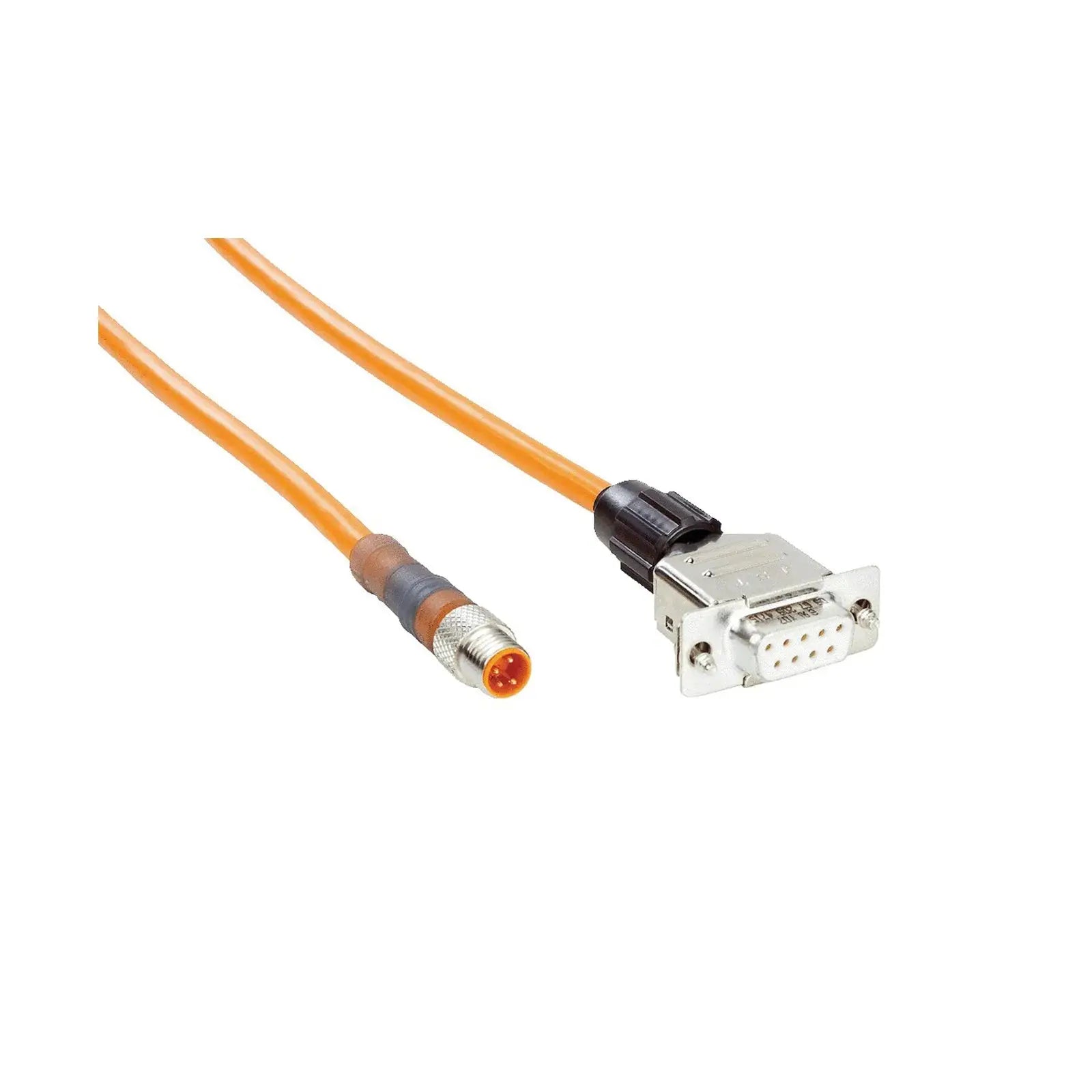



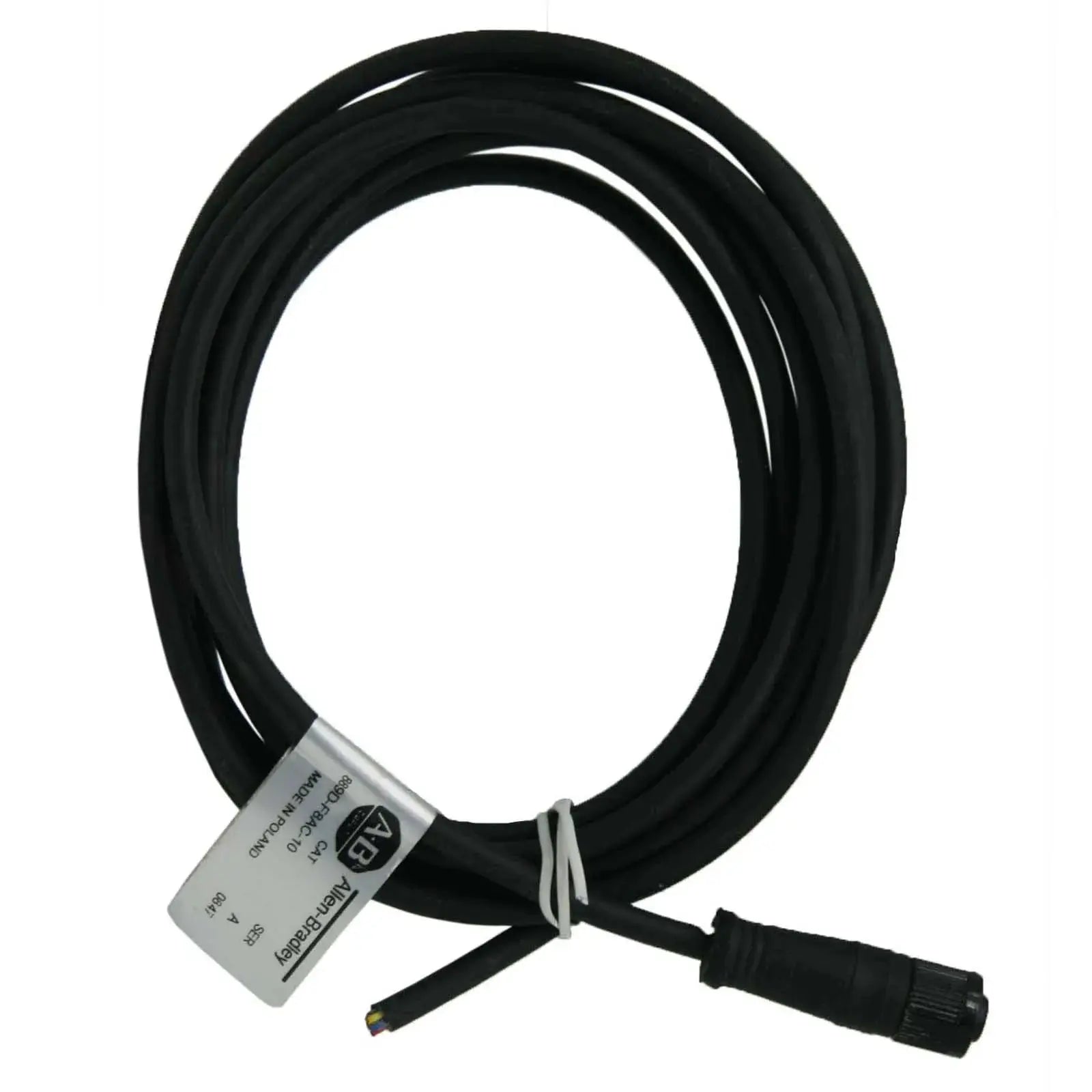

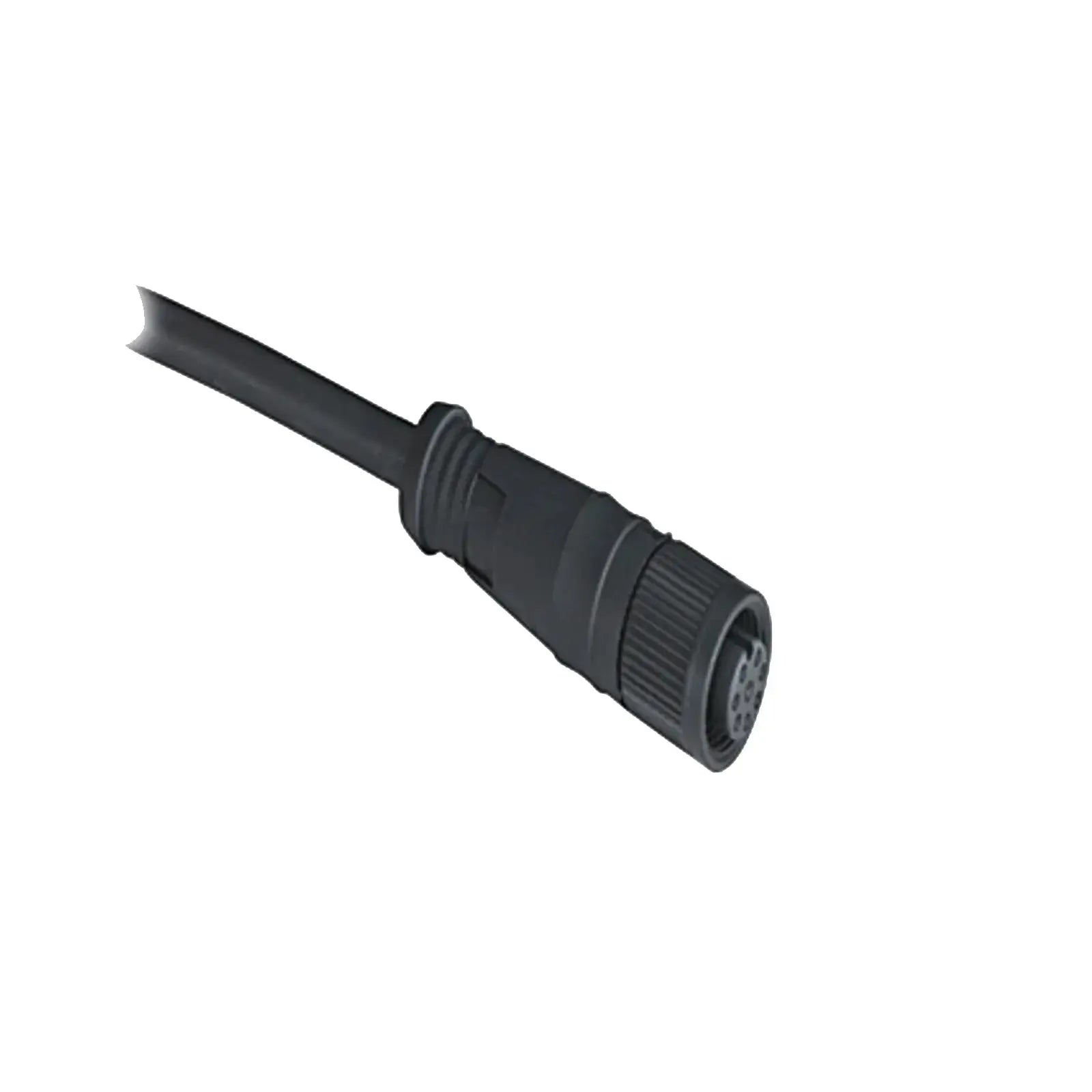

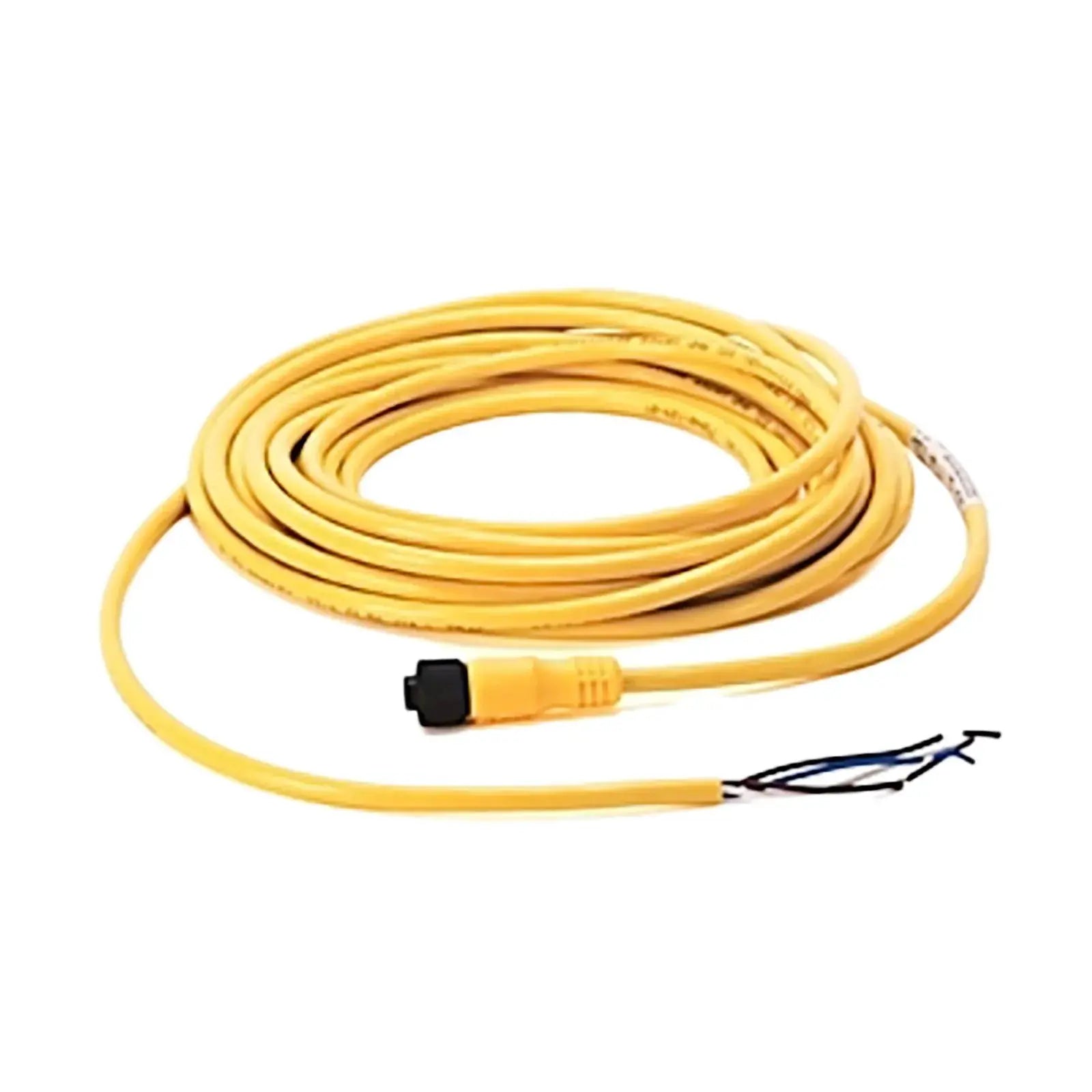

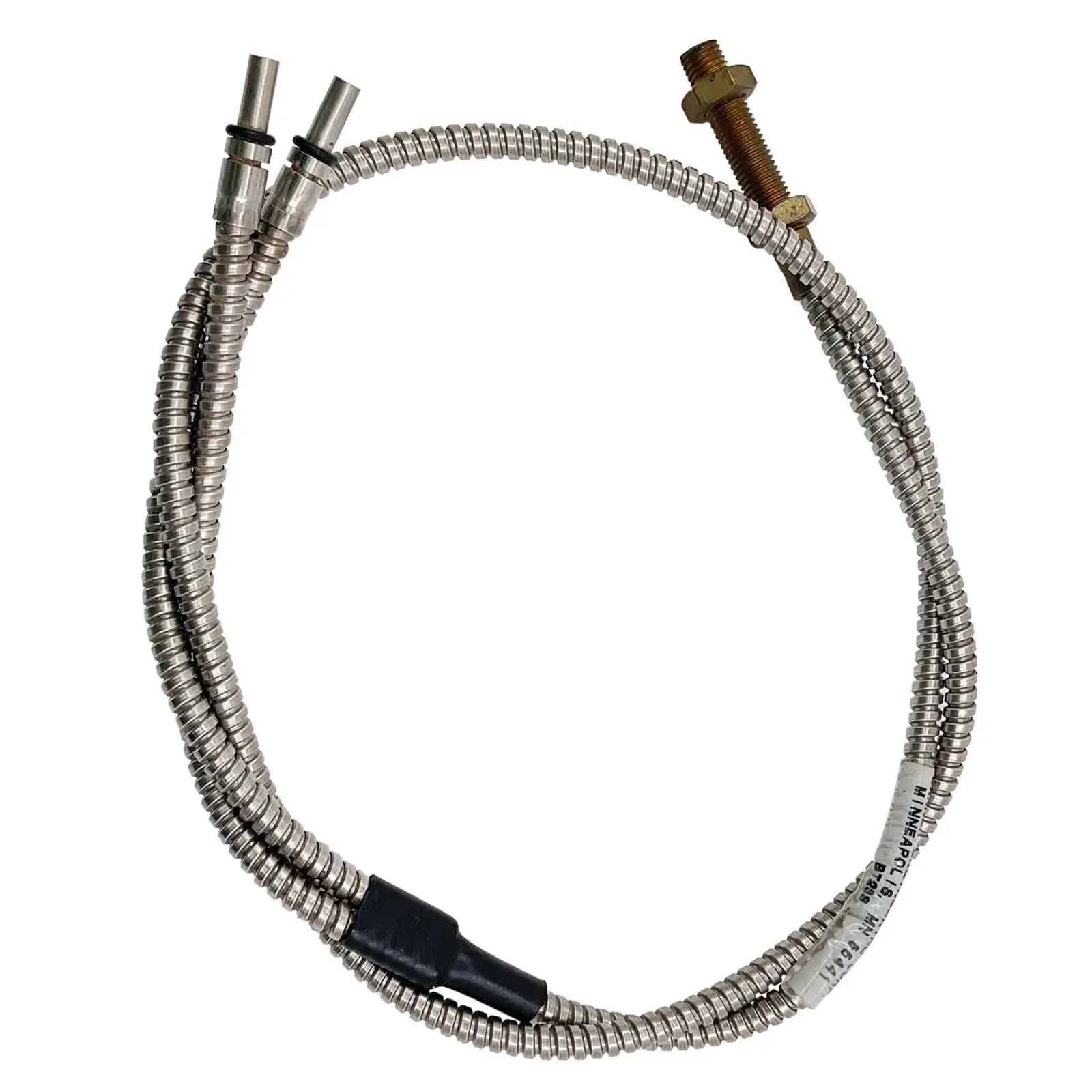
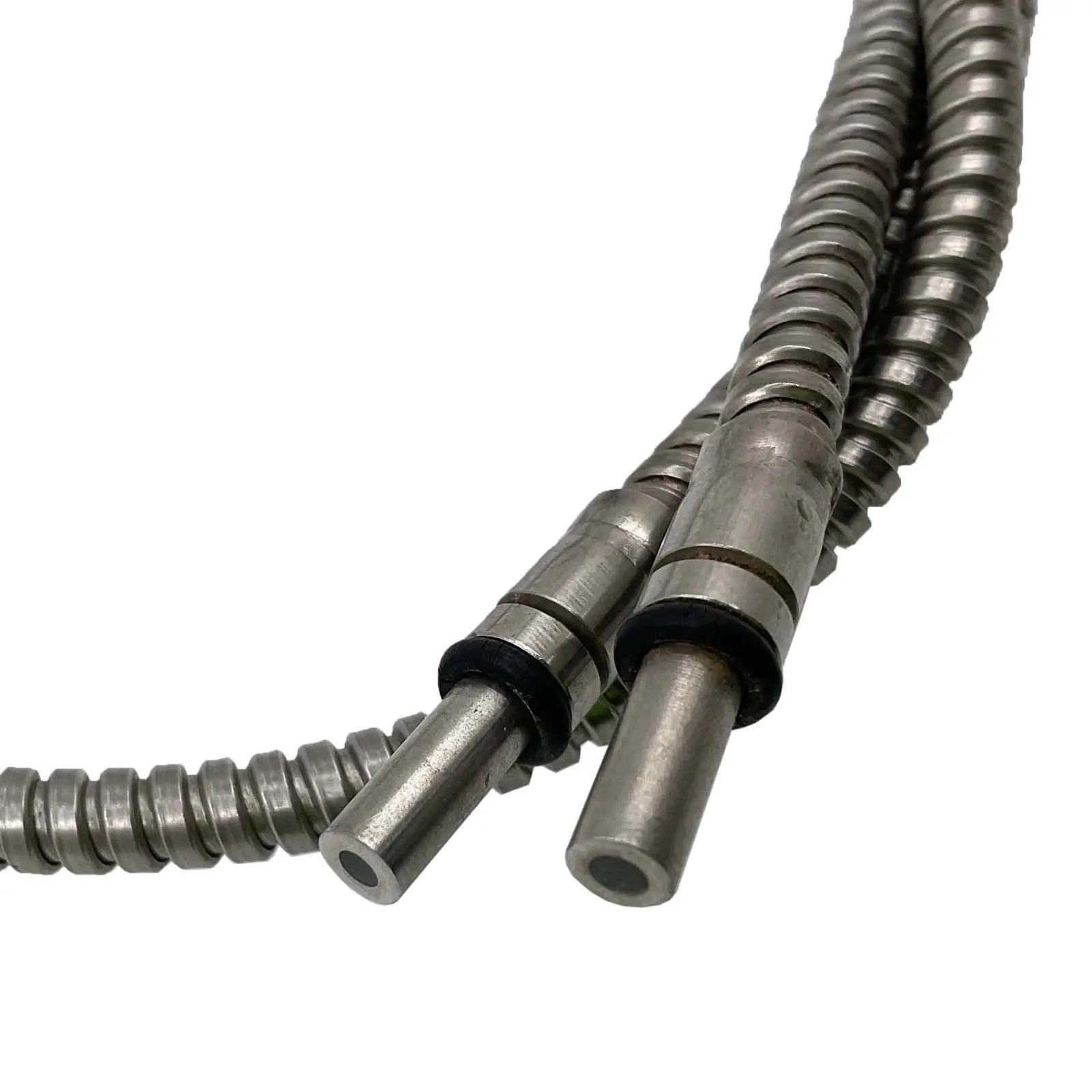
High-Performance Sensor Cables for Reliable Connectivity
Explore our wide range of Sensor Cables designed to deliver reliable and accurate signal transmission in industrial automation, control systems, and machinery applications. Built for durability and precision, these cables ensure stable connections between sensors and control units, even in demanding environments. Our collection includes a variety of lengths, connector types (such as M8, M12), and configurations (straight, angled, 3-pin, 4-pin, etc.) to suit diverse installation needs. Whether you're working in manufacturing, robotics, or process control, our sensor cables offer excellent resistance to oil, moisture, and mechanical stress, ensuring uninterrupted performance and long service life.
Each cable is crafted to meet industry standards, providing secure locking mechanisms and plug-and-play convenience for quick and reliable setup. From standard signal transmission to more specialized sensing requirements, you’ll find dependable solutions right here.
Need Bulk Orders or Expert Recommendations on Sensor Cables?
Looking for bulk sensor cables orders or need help choosing the right industrial solution? Our team is here to assist with custom quotes, product recommendations, and technical guidance. Whether you're an electrician, contractor, or business owner, we offer tailored solutions to meet your needs.
📩 Contact Us or chat with us live for instant assistance!
Explore Our Monthly Madness Deals Collection!
Don't miss out on **huge savings** across our store! Check out the best deals in:
Explore these categories now and grab the best deals before they're gone!
- All Products in Our Range – Top-quality products handpicked for you.
- Best Sellers – Customer favourites and high-demand items.
- Watts Hot Deals and Sales – Limited-time discounts on must-have products.
- Watts New – Fresh arrivals and the latest innovations.
-
All Collections – Explore everything we have to offer.
Explore these categories now and grab the best deals before they're gone!
Don't forget to Check out our Massive Markdowns While Stocks Last!
Recently viewed
Watts Current Newsletter
Stay connected with the latest industrial electrical products, exclusive deals, and expert updates.
Sign up now and never miss out