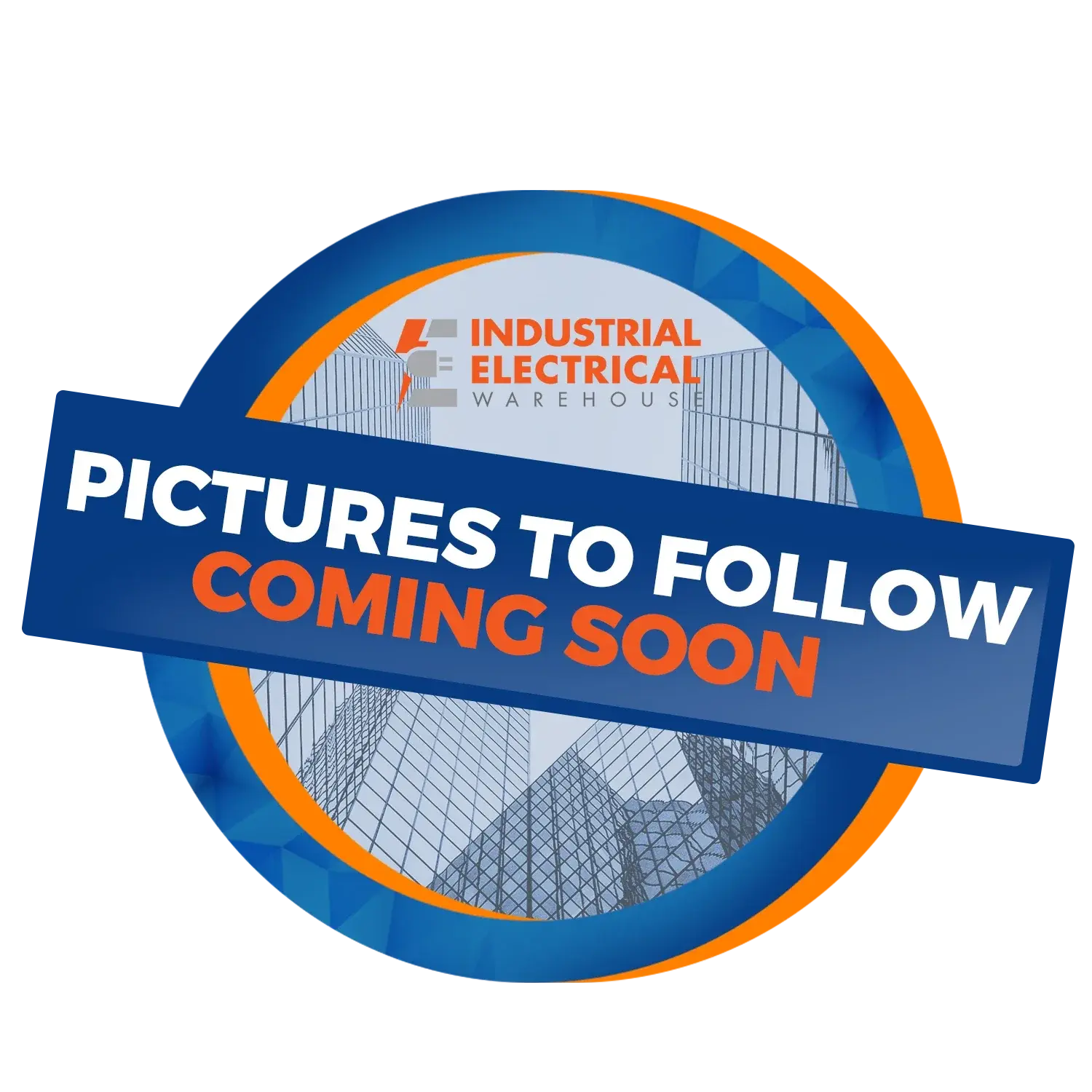
Control Gear
12 products
Showing 1 - 12 of 12 products
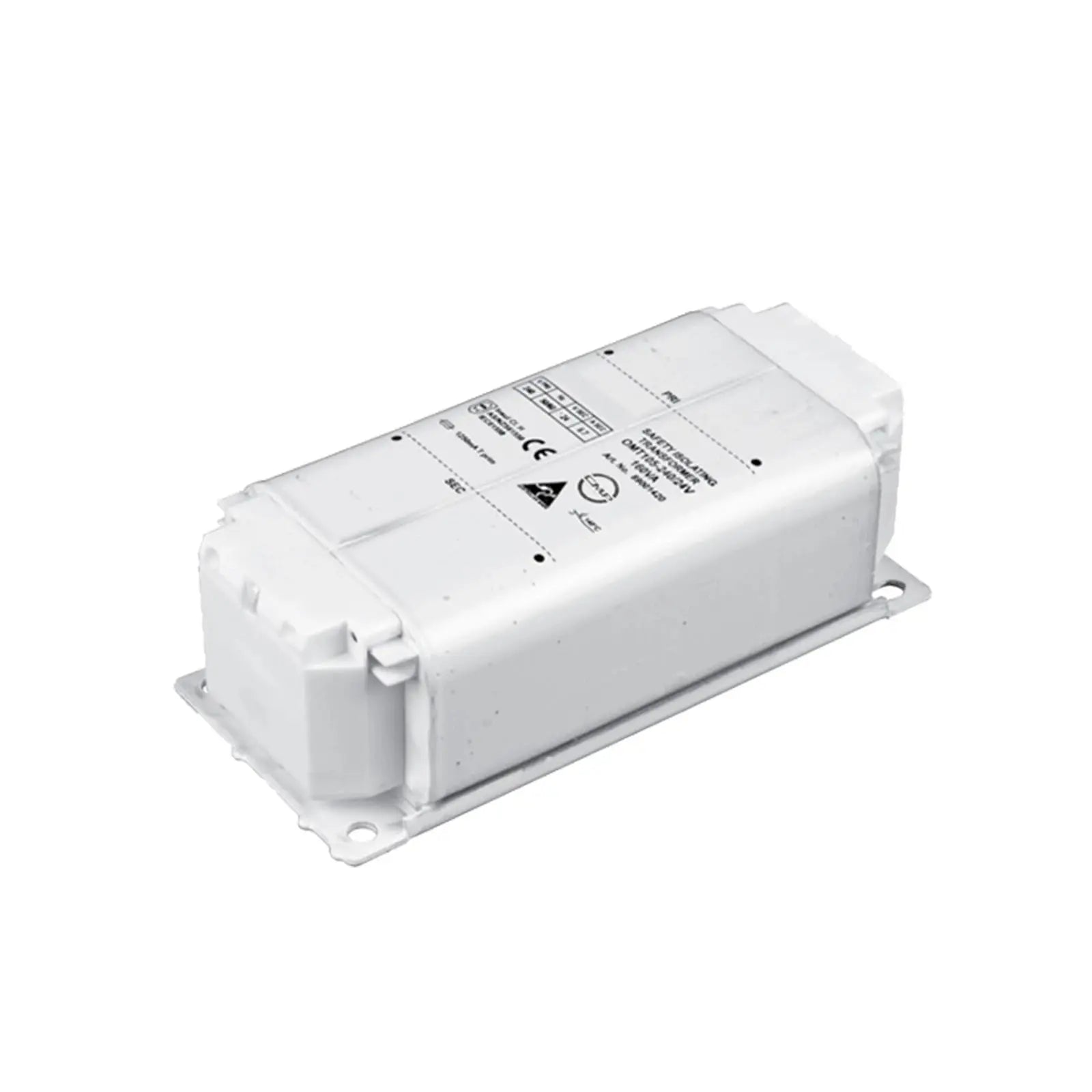
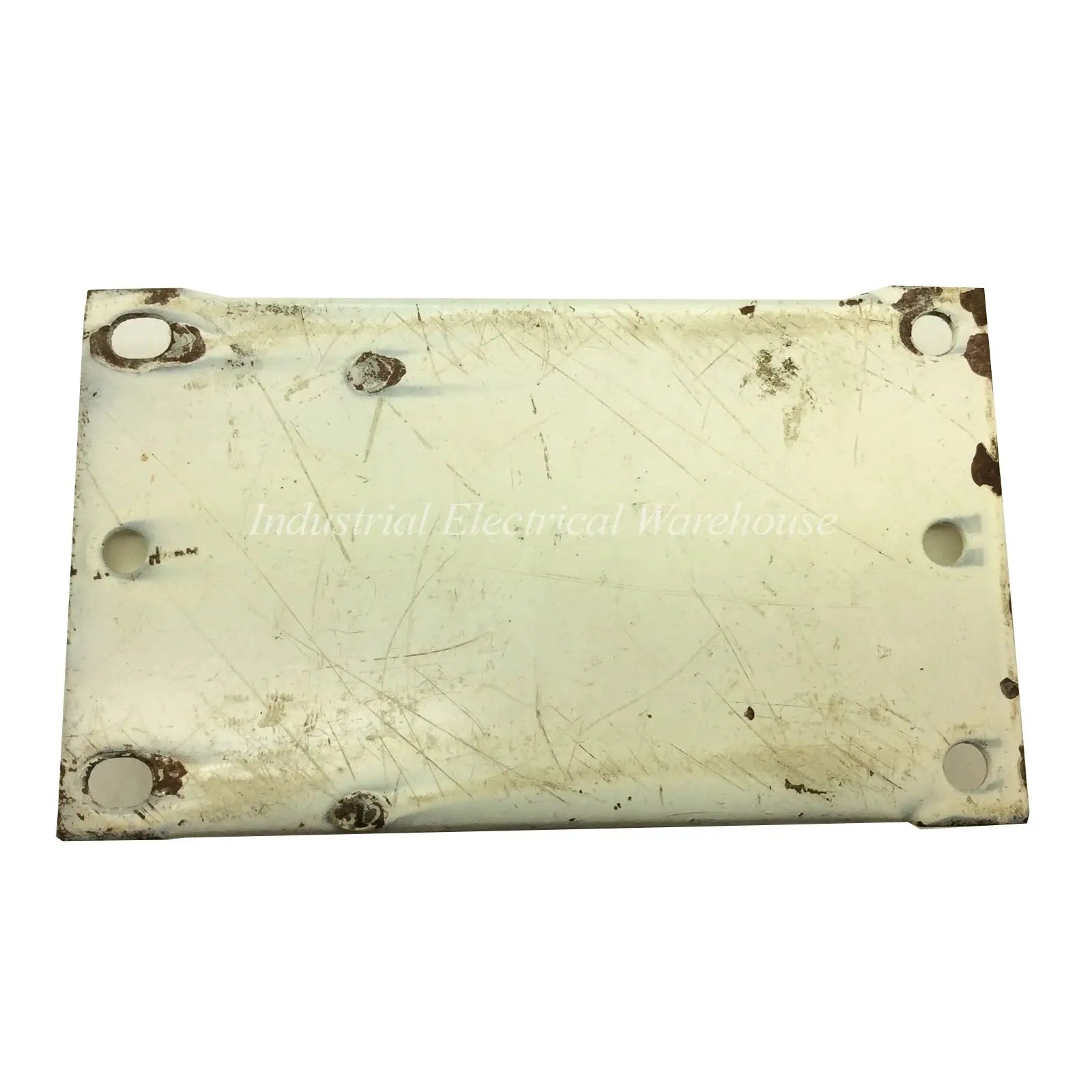


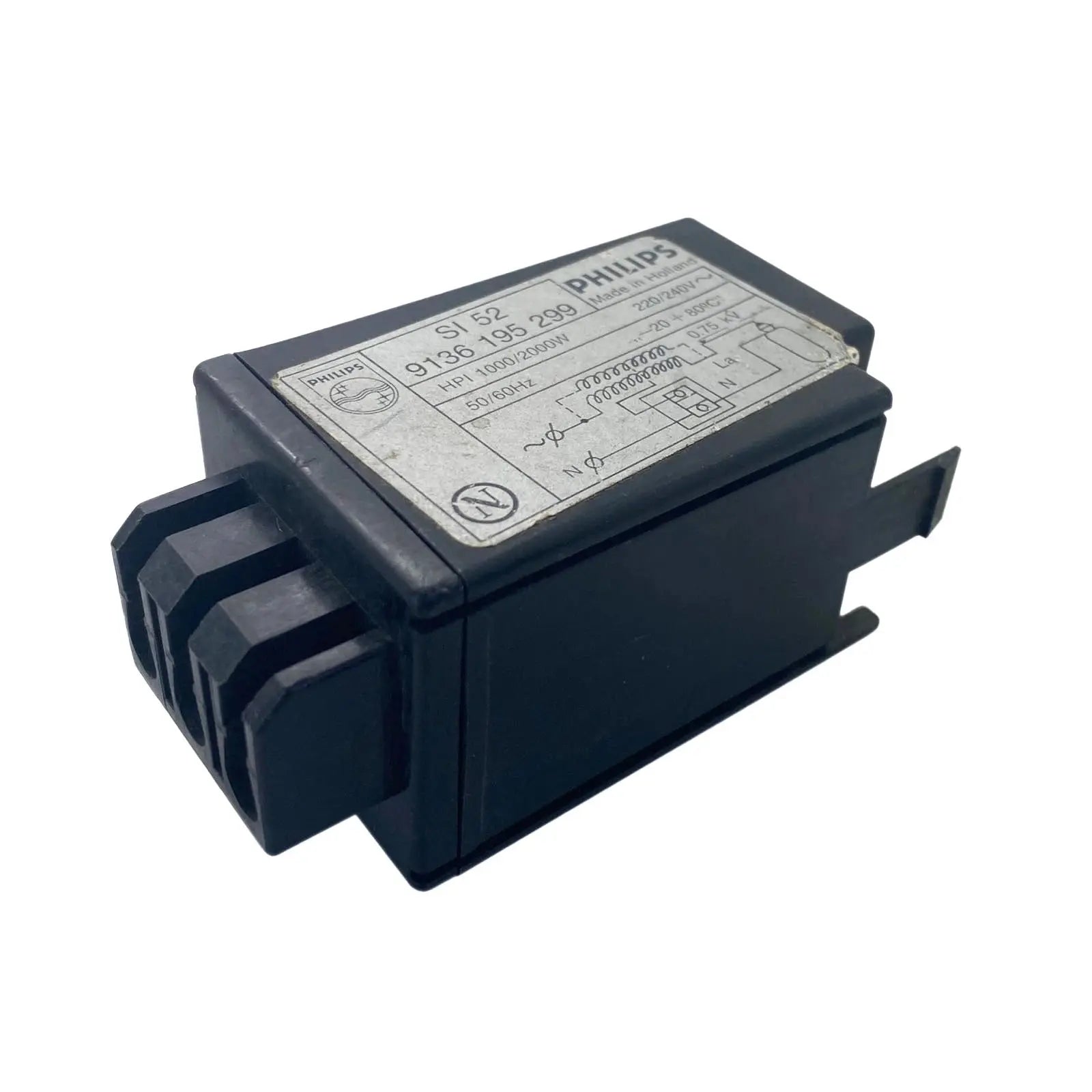
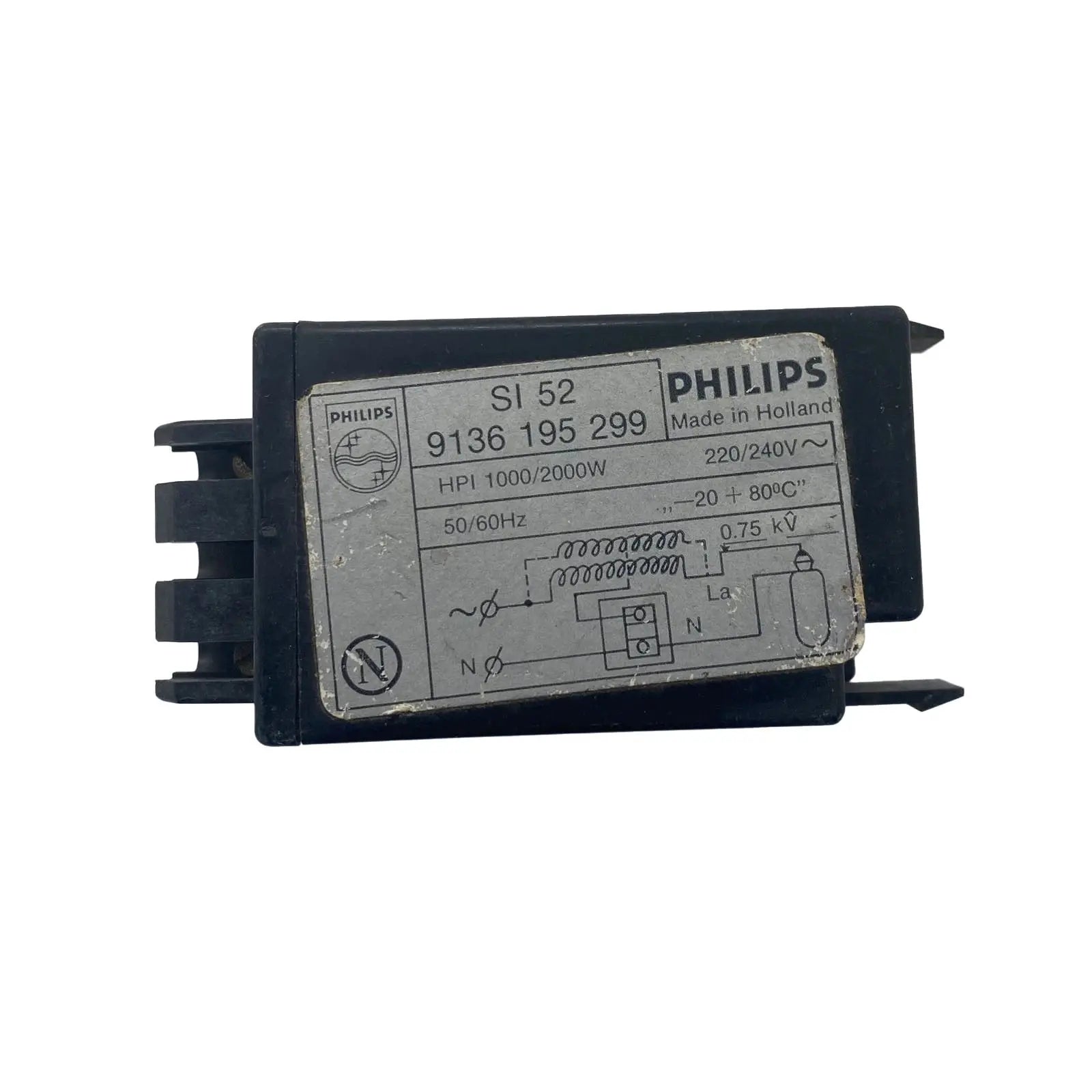
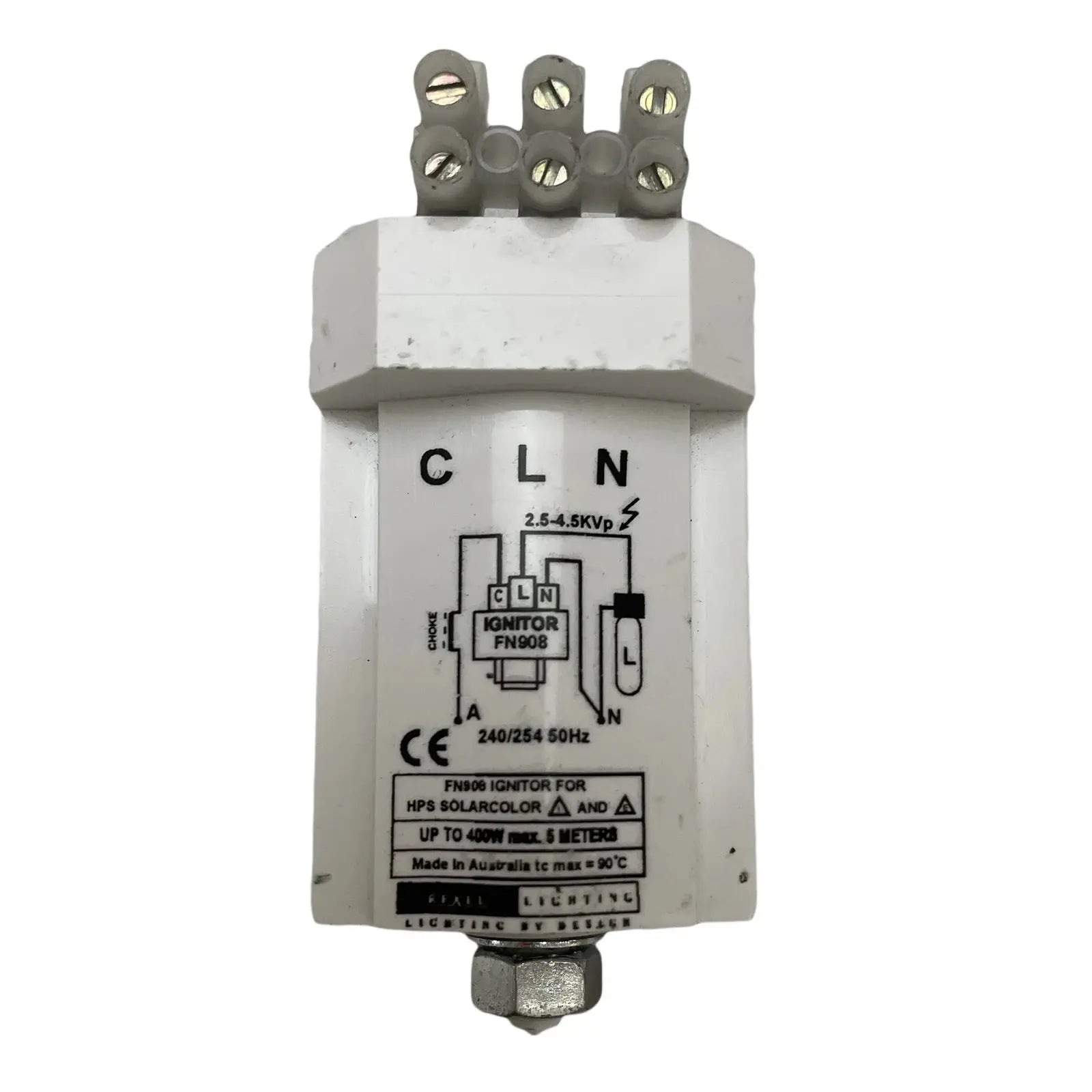
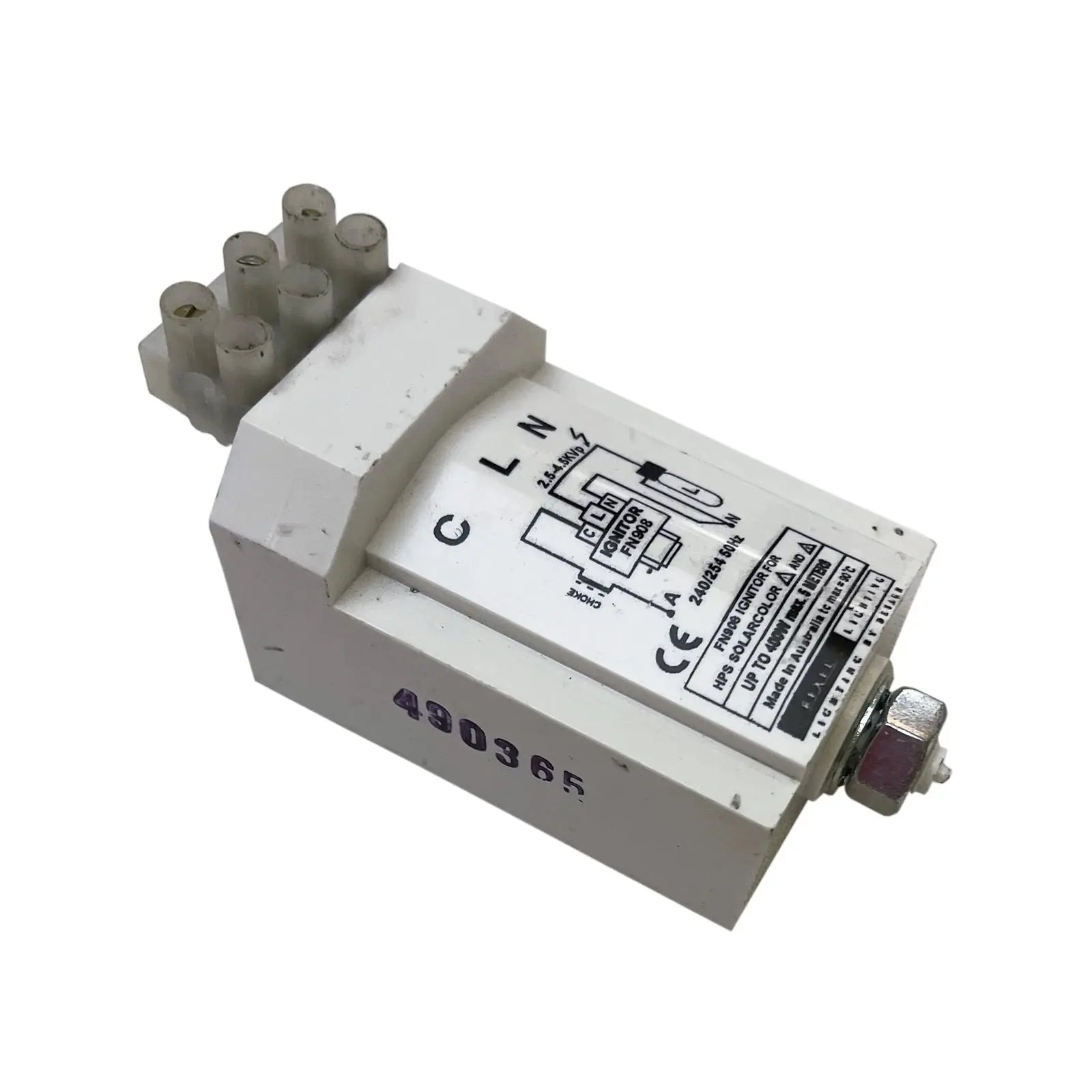
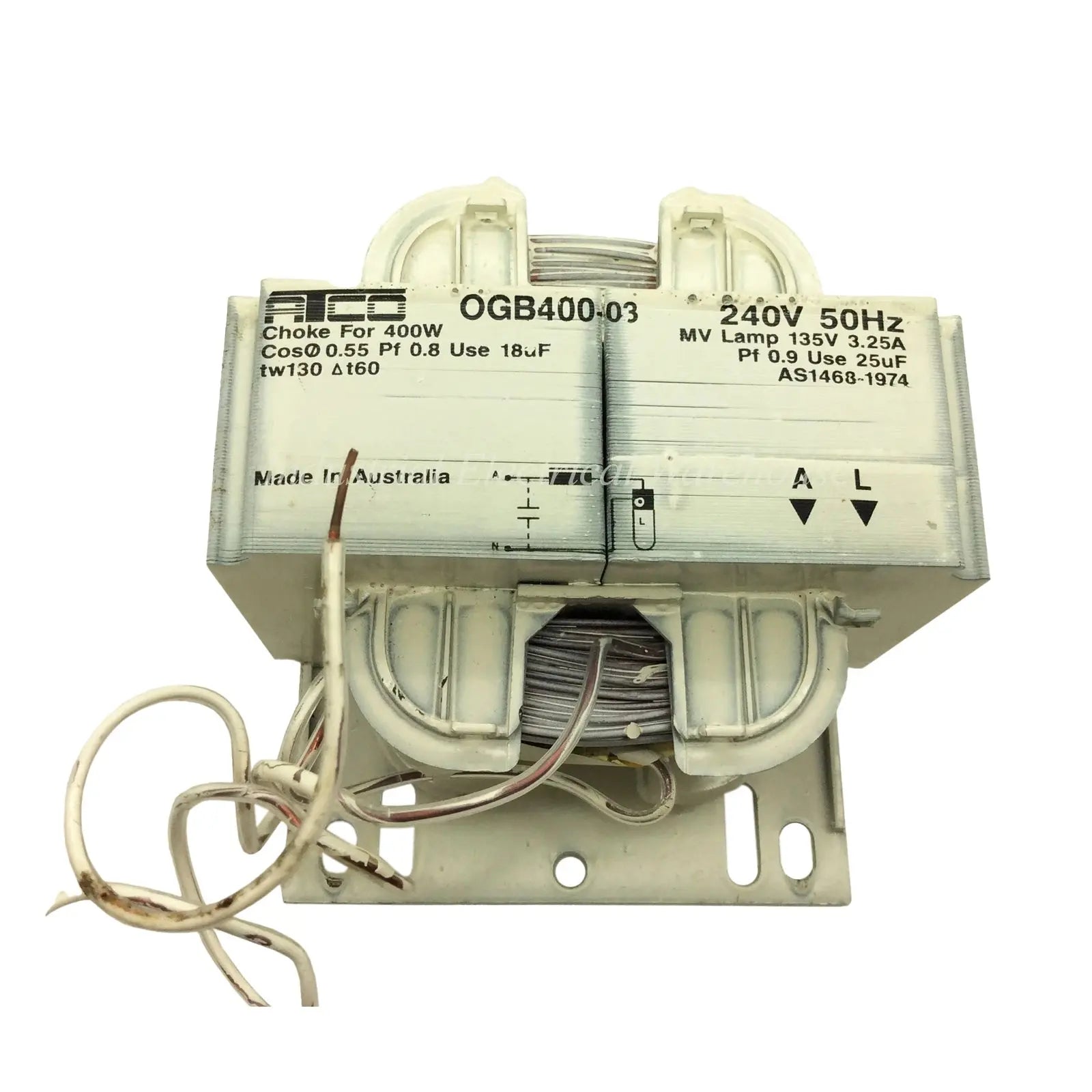
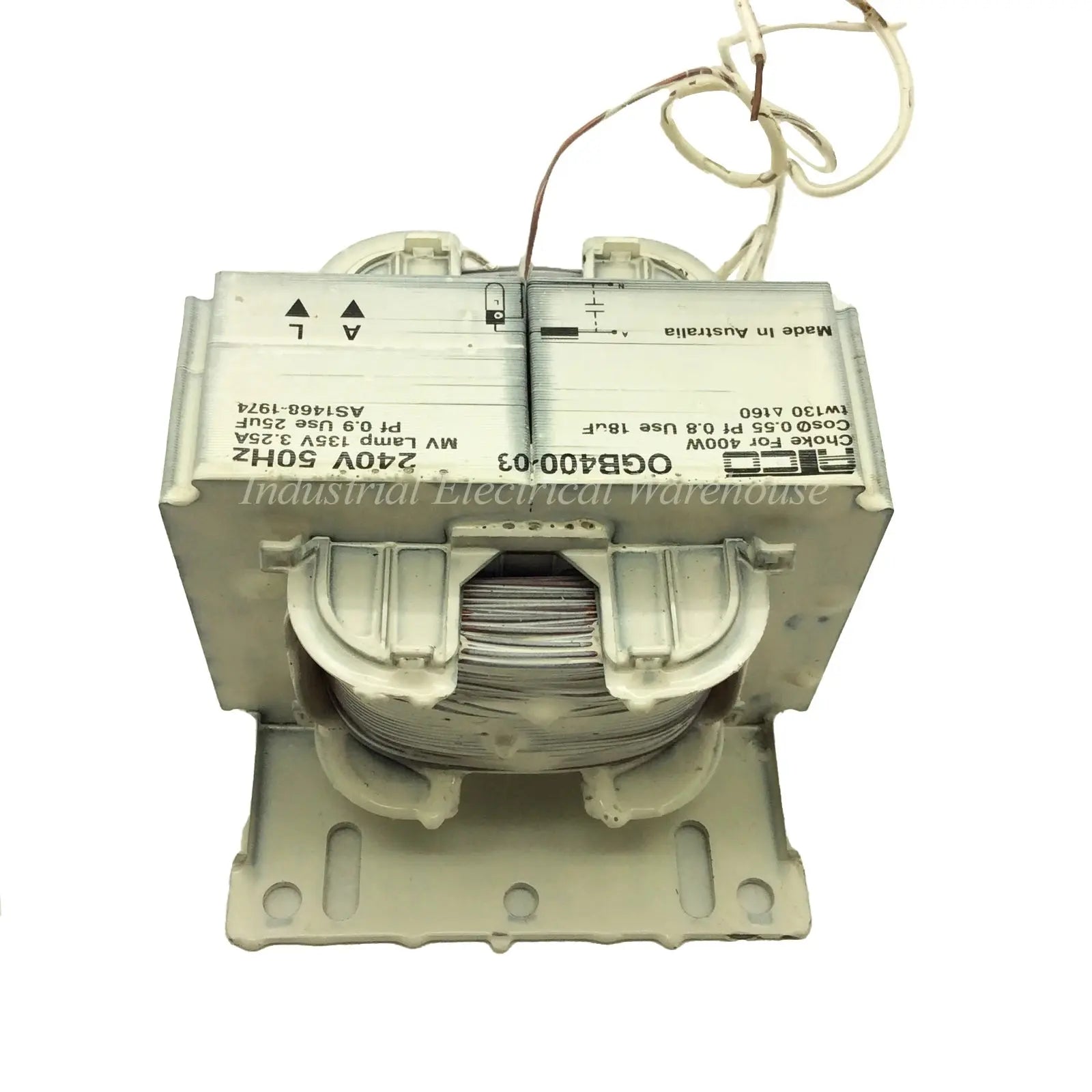

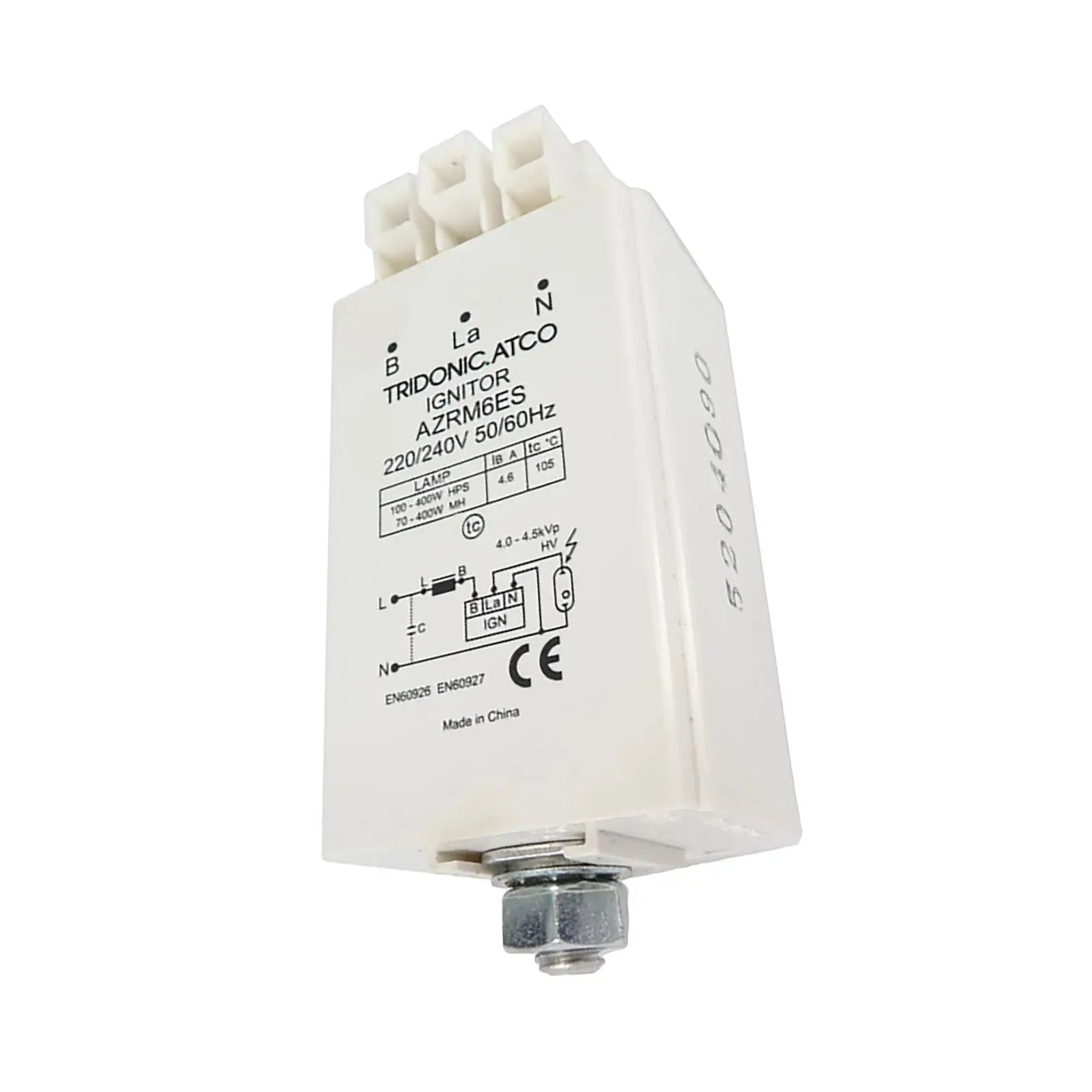
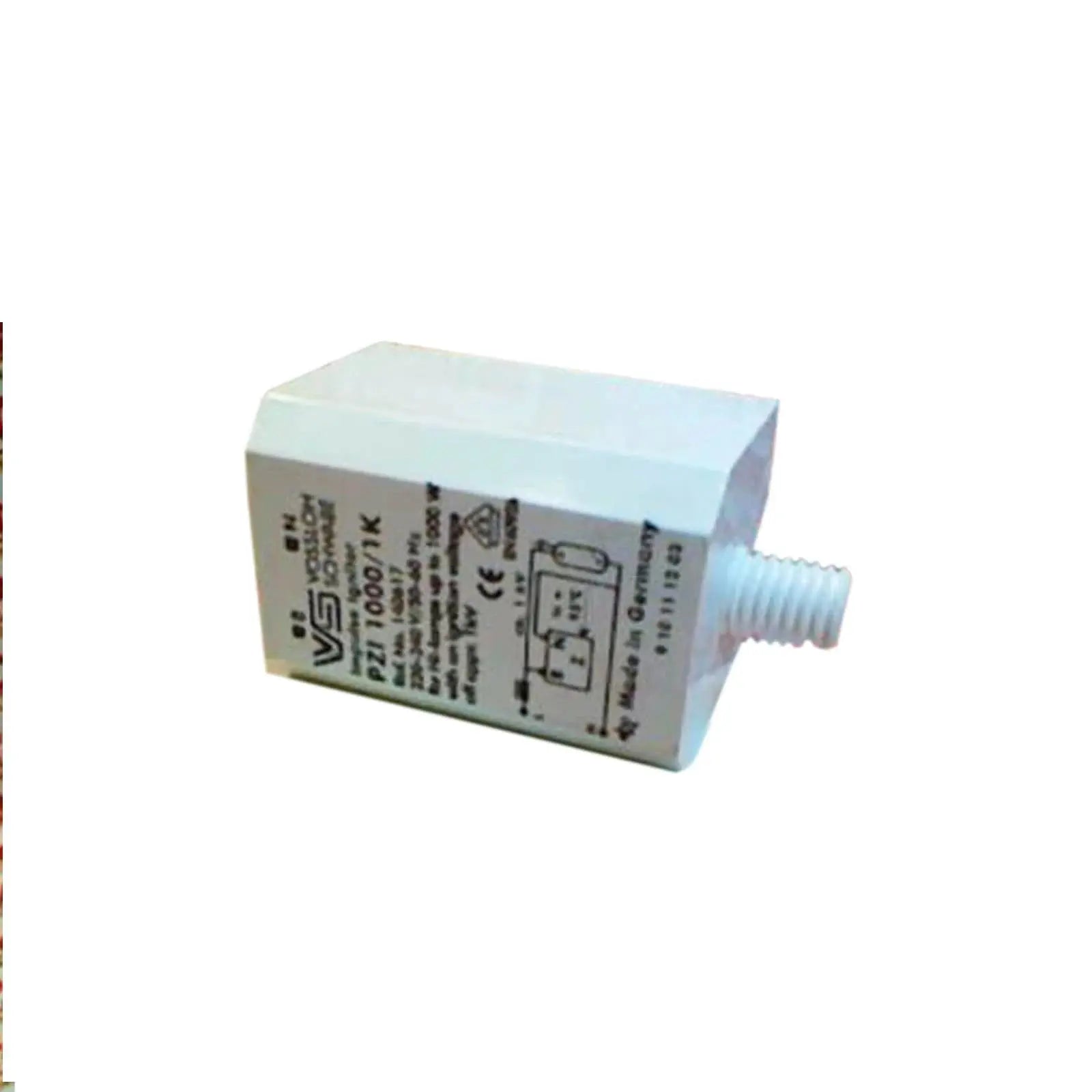
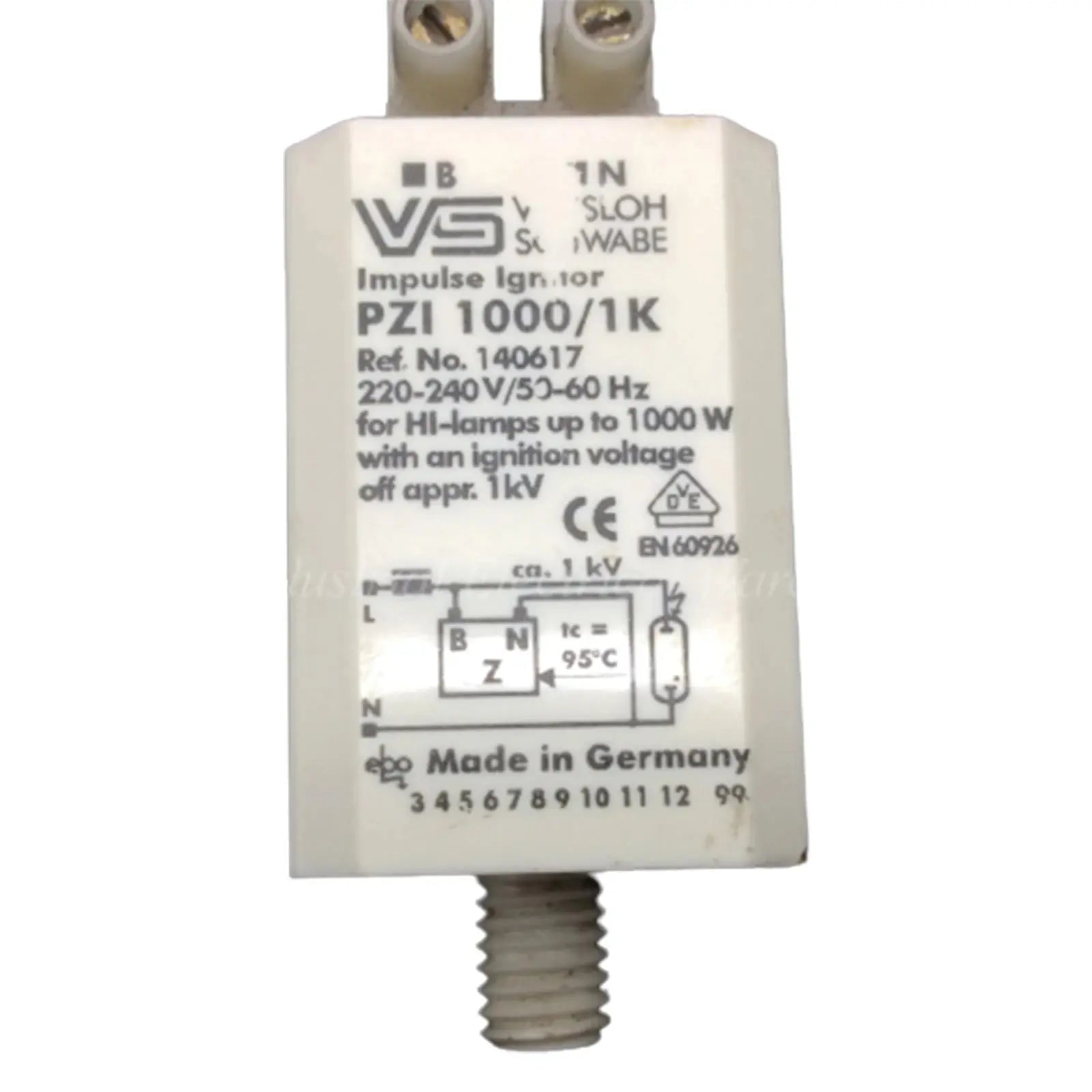
Control Gear – Reliable Electrical Control Solutions
Control gear refers to the essential devices and components used to manage, regulate, and protect electrical equipment. From motor starters to protection devices, control gear ensures that machinery and systems operate safely and efficiently. Our collection features products suitable for industrial, commercial, and automation applications, offering dependable performance in a wide range of environments.
How Does Our Control Gear Ensure Performance and Safety?
Each control gear product is engineered to meet strict industry standards, providing precise control, effective protection, and long-term durability. Designed with high-quality materials and advanced technology, they are capable of withstanding demanding operating conditions while delivering consistent results.
Need Bulk Orders or Expert Recommendations on Control Gear?
Our team can provide technical guidance, custom quotes, and product recommendations to match your project’s requirements. Whether you’re managing a small installation or a large industrial system, we have the right control gear solutions for you.
📩 Contact Us or chat with us live for instant assistance!
Explore Our Monthly Madness Deals Collection!
Don't miss out on huge savings across our store! Check out the best deals in:
Explore these categories now and grab the best deals before they're gone!
- All Products in Our Range – Top-quality products handpicked for you.
- Best Sellers – Customer favourites and high-demand items.
- Watts Hot Deals and Sales – Limited-time discounts on must-have products.
- Watts New – Fresh arrivals and the latest innovations.
-
All Collections – Explore everything we have to offer.
Explore these categories now and grab the best deals before they're gone!
Don't forget to Check out our Massive Markdowns While Stocks Last!
Recently viewed
Watts Current Newsletter
Stay connected with the latest industrial electrical products, exclusive deals, and expert updates.
Sign up now and never miss out